In enhancing your work environment, understanding 'what are the four barriers to change' becomes critical to fostering innovation and ensuring growth.
Lack of Knowledge about the Benefits of Change
Too common their can be a misunderstanding about the intent of change projects. New innovation has the potential to improve quality and production speeds, but operators' mindsets may not recognize the improvement of their daily tasks. Ignorance of this can result in a reluctance to embrace effective changes.
- Change can lead to reduced fatigue by eliminating tasks, allowing greater throughput with less effort.
- Heightened assembly precision leads to fewer defects, reducing the frustration associated with rework.
- Innovation can enable assemblers to expediently tackle complex projects, hence widening the range of assignments they can accept.
- Change initiatives can carry the potential for increased profitability and market competitiveness. Though this one is often expected, knowledge about how the company plans to reinvest in it's work culture can go a long way in improving the execution of the change project.
Resistance to change
Implementing a transition strategy that addresses the fear of change can be beneficial. Conducting workshops, providing counseling, and offering reassurance aids in mitigating the fear of job security. These actions will enable a successful transition towards new practices and technologies.
Embracing innovation in manufacturing enhances production efficiency, fosters a culture of learning, and, ultimately, leads to company growth.
Fostering a culture of innovation is key in overcoming resistance in manufacturing. Supporting open dialogue, encouraging risk-taking, and rewarding innovative ideas helps to dispel skepticism. It also promotes a culture whereby workers are eager to adopt new methods and technologies, contributing positively to company growth.
Fear of job loss or reduced job security
For many folks working in the assembly industry, fear of job loss or decrease in job security often hampers the acceptance of innovative technologies. However, contrary to these concerns, embracing technological progress can actually fortify job security, carving out a new terrain for fresh opportunities and advanced skills.
- Technological advancements in the assembly industry often create more nuanced roles that require new skills, potentially providing enhanced job security and steadiness.
- Innovation often equates to efficiency, potentially reducing the threat of downsizing due to poor productivity.
- By staying updated with the latest technologies, workers can become more valuable to the organization, fostering greater job security.
Attachment to familiar routines and processes
While the comfort of familiar processes can create a sense of security for assemblers and fabricators, it can also impede innovation. Breaking free from traditional routines is a critical step in facilitating cutting-edge development on the assembly line.
- Acknowledge the effectiveness of existing processes
- Emphasize the benefits of innovation
- Implement incremental changes to ease the transition
- Promote a culture of continuous learning and improvement
- Provide support and training during the transitional period
- Celebrate the success of new implementations
Inadequate resources and infrastructure
Outdated resources and technologies often create a bottleneck, stalling progress and innovation in assembly operations. Overcoming this requires proactive investments in modern tools and equipment.
Infrastructure challenges may hold back the evolution of manufacturing operations. By systematically addressing these, organizations can build a solid foundation that accommodates and champions change.
Lack of financial resources for investment in new technology
Understanding the investment returns of new technology in the assembly industry is essential. This knowledge builds a convincing case for the infusion of capital into tech-enhancements, driving efficiency, and boosting productivity.
Strategically streamlining budgets to accommodate technology finance can lead to monumental shifts. It not only empowers assembly workplaces with the latest innovations but also enhances value on production lines, attracting more customer attention.
Obsolete or insufficient equipment and tools
Progress in assembly is often thwarted by the use of outdated equipment. Not having access to cutting-edge tools can significantly hamper productivity and the ability to adapt to the ever-evolving industry standards.
Revamping the assembly line tools stands as a viable solution to overcome resistance to change. By investing in new, optimal equipment, companies can streamline operations and inspire confidence in their workforce.
However, it's crucial to manage such transitions effectively, ensuring all personnel are adequately trained to use these advanced tools and technologies. Seamless integration of new apparatus can invigorate the workforce, creating a dynamic environment ready to embrace change.
Organizational culture and structure
In a manufacturing environment, a rigid organizational culture can stifle innovation, broadly impacting the pace of change adoption. Without managerial encouragement or support, employees might resist implementing new techniques, stunting growth.
Embracing change within a factory often calls for a structural overhaul. Hierarchical structures that limit the flow of communication and collaboration may need to be flattened, fostering an atmosphere of openness, and in turn, prosperity.
Lack of support and encouragement from management
A challenging barrier in the assembly sector could be unintentional – emanating from weak leadership. Management's lack of encouragement and support hampers the development and adoption of innovative practices, hence stifling change.
However, a turnaround can occur when managers actively foster change. As catalysts, they can inspire their team towards an assembly transformation, stirring up enthusiasm and commitment towards technological adaptations and process innovations.
Hierarchical structure inhibiting communication and collaboration
Utilizing cross-functional teams and open forums can break down rigid hierarchies, fostering enhanced communication and collaboration. Providing platforms for open communication encourages fresh idea exchange, thus driving innovation and adaptive change.
Agile hierarchy, a flexible management system, positively impacts assembly practices. Through enabling quick decision-making, promoting regular feedback, and fostering a culture of continuous learning, it aids in the successful implementation of new technologies and efficient methodologies.
Resistance from employees
Employee empowerment serves as a pivotal ingredient for change acceptance, yet, an alarming resistance often trails it within assembly contexts, stifling innovation. Fostering an environment of skepticism, employees tend to challenge change initiatives because they perceive an impending surge in workload and increased pressure.
Skepticism and mistrust towards change initiatives
Debunking change-related misconceptions in assembly becomes critical as it's often the misinformation that fuels skepticism. Highlighting the factual benefits of innovation with tangible evidence can silence distrust and ignite excitement for advancement.
Building trust in innovation is crucial because adoption breeds on belief. Assemblers and fabricators taking the lead to engage in informative dialogues, workshops or seminars about the change can provide a reassuring platform for acceptance.
Perceived increased workload or pressure
The perception of change as a workload enhancer needs to be shifted. Instead, it should be portrayed as a stress-reliever, automating painstaking tasks and allowing workers to focus on valuable functions.
Resistance due to fearing increased work can be mitigated through explicit communication. Making the workers understand how innovative technology can distribute work evenly and reduce pressure is crucial.
The journey from resistance to receptiveness lies in systematically managing workload apprehensions. Showcasing how new assembly methods can simplify tasks and reducing the fear of work overloads will lead to acceptance of change.
Lack of clear goals and vision
Eradicating ambiguity is intrinsic to successful change, especially in assembly. Defined goals not only showcase the end target but effectively illustrate the trajectory, enabling preparation, anticipation, and adaptation.
A clear vision aids change resilience, addressing uncertainty issues. It lights the path to the future, outlining what is expected and why. This fosters trust, acceptance, and commitment, acting as a formidable catalyst in assembly innovation.
Uncertainty about the desired outcomes of change
In an industry that is entrenched in precision, the uncertainty that accompanies change can seem daunting. Assemblers who fail to foresee the ultimate outcomes of alteration often hesitate to adapt, affecting the overall receptiveness to innovative tactics.
Unfamiliarity with the possible repercussions of updates often triggers skepticism. This sense of unpredictability, in an otherwise precise and meticulous domain, generates an inertia that hinders growth and advancement.
Lack of a compelling vision for the future
Embedding a vision into change initiatives can dissipate fear due to inevitable changes, directing assemblers towards positive outcomes. This helps them view potential change as an opportunity rather than a threat.
A future-oriented vision is the linchpin for real transformation in a factory. It provides a roadmap, communicating the significance of change and showcasing benefits that await post-transition.
However, clarity needs reinforcement. Consistent support from leadership helps keep employees engaged, maintaining momentum towards the envisioned future and ensuring the successful implementation of the change initiative.
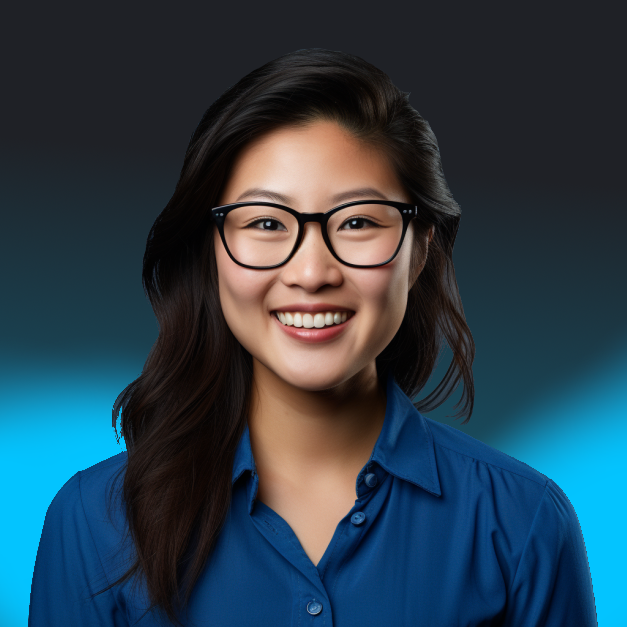
Jen Moore
I absolutely LOVE being outside. Being a soccer enthusiast and a dog mom, I spend much of my free time running with my pups or kicking a ball with my team.