Imagine your production line slowed down by outdated machinery. Is efficiency being compromised by legacy systems?
It's an increasingly common scenario. Manufacturers utilizing old equipment struggle to keep up with competitors, facing downtime and diminished product quality. However, there's a transformative shift underway with the adoption of modern Press Brakes, Lasers, and Plasmas, ushering in unparalleled precision and productivity. Adopting these technologies isn't just an upgrade, it's a leap into the future of manufacturing excellence.
Revolutionizing Metal Fabrication
The implementation of cutting-edge industrial equipment represents a monumental stride in metal fabrication. These modern tools offer not only increased accuracy but also augmented speed and efficiency. This leap forward not only elevates product quality but also significantly enhances operational throughput, ensuring that assemblers and fabricators remain at the forefront of industry innovation.
Embracing the advancements in these key areas of metalworking involves an essential recalibration towards smart manufacturing practices. This includes the integration of sophisticated data collection systems, which enable real-time monitoring and adjustments, ensuring optimal performance across the production floor. By replacing legacy equipment with these contemporary solutions, fabricators can deliver superior products with greater consistency, fostering not just satisfaction but admiration in their customers.
Press Brake Innovations
Modern Press Brakes epitomize precision with CNC-controlled bending operations, enhancing product consistency and reducing scrap rates at a remarkable pace. Integrating advanced software enables finer control over complex bends, thus meeting the high expectations of today's markets.
Innovation in Press Brake technology extends to real-time angle corrections, creating a process best described as "adaptive bending." This ensures parts are perfectly shaped from the first run, saving time and resources while boosting overall performance.
Press Brake tooling evolves with materials, pushing bends to perfection.
Adaptive bending also supports the eco-friendly paradigm shift, where energy efficiency complements raw power. By upgrading to these intelligent systems (which excel in precision and speed), assemblers and fabricators not only refine their production line but can also share a narrative of sustainability with their clients. This aligns well with a market that increasingly values environmental consciousness.
Laser Cutting Advancements
Laser cutting technology has burgeoned, directly enhancing productivity and precision.
- Fiber lasers offer greater efficiencies and faster cutting speeds.
- Automation integration allows for reduced operator intervention.
- Predictive maintenance software preemptively addresses potential machine failures.
- Enhanced optics improve the focus and quality of the laser beam.
- Real-time monitoring systems ensure ongoing process optimization.
These advancements result in shorter lead times and consistent high-quality cuts.
Investing in modern laser systems is imperative for staying at the forefront of manufacturing excellence.
Plasma Technology Upgrades
Upgrading to advanced plasma systems enhances precision, speed, and efficiency.
- High-Definition Technology significantly improves the cut quality and detail.
- Automated Control Systems yield precise cuts with minimal operator input.
- Faster Cutting Speeds translate to increased throughput.
- Consumable Optimization reduces replacement frequency and operational costs.
- Integration with CAD/CAM Software streamlines the workflow from design to execution.
The transition to modern plasma systems represents a strategic imperative.
Embracing these upgrades positions fabricators at the cutting-edge of manufacturing.
Boosting Factory Productivity
Legacy equipment often acts as a bottleneck in the flow of production, imposing limitations on speed and precision. Conversely, advanced press brakes, lasers, and plasmas carry the potential to revolutionize throughput. Incorporating these technologies ensures products meet stringent quality standards while allowing for rapid scale in operations.
Transitioning to contemporary systems is not a mere upgrade; it's a transformative step. Factories harnessing the dynamic capabilities of these modern machines can attain unmatched levels of efficiency. The digitization and automation these systems offer are yielding veritable leaps in factory productivity.
Downtime Reduction Techniques
Predictive maintenance is integral to minimizing unexpected breakdowns and production halts. By leveraging data analytics, manufacturers can preemptively identify and rectify potential issues before they escalate to costly downtime.
With the implementation of real-time monitoring systems, modern press brakes, lasers, and plasmas become profoundly more reliable. These systems provide continuous feedback, facilitating immediate troubleshooting and maintenance. Manufacturers can thus prevent lengthy disruptions, ensuring ongoing production and timely delivery of products. This level of responsiveness to machinery health is foundational in maintaining a competitive edge.
Streamlined component interchangeability within advanced equipment sets is another pillar in reducing downtime. By designing machines with standardized parts, manufacturers facilitate quicker replacements and repairs. The resulting efficiency not only shortens downtime but also simplifies inventory management, reducing the need for extensive stockpiles of specialized components.
Moreover, the integration of modular design philosophies across press brakes, lasers, and plasmas empowers quick adaptability and on-site modifications. Rather than extensive downtime for major overhauls, modular design allows for incremental upgrades and changes. This approach ensures that equipment evolves with technological advancements, maximizing productivity and extending the lifecycle of the capital investment. Such foresight reflects highly on manufacturers prioritizing uptime, directly translating to increased customer satisfaction and loyalty.
Data Integration
Data integration is pivotal for maximizing the efficiency of modern industrial equipment.
- Real-Time Monitoring: Continuous data flow allows for immediate adjustments and quality control.
- Predictive Maintenance: Anticipate equipment failure by analyzing operational data trends.
- Process Optimization: Utilize collected data to streamline and refine manufacturing processes.
- Energy Management: Monitor and adjust energy consumption for cost-saving and sustainability.
- Compliance Tracking: Ensure all operations remain within industry standards and regulations.
Seamless communication between machines augments production intelligence.
Intelligent data utilization can provide a substantial competitive advantage in manufacturing environments.
Enhancing Precision and Quality
The integration of advanced press brakes, laser cutting, and plasma cutting technologies represents a monumental leap in fabrication precision and product quality. Eclipsing their legacy counterparts, these modern systems work with near-micron level accuracy, facilitating the meticulous creation of complex components with unparalleled repeatability. This precision not only enhances the aesthetic and functional qualities of finished products but also significantly reduces material waste.
Current advancements in equipment technology are redefining industry benchmarks for quality and precision. Assemblers and fabricators employing these state-of-the-art tools can assure customers of exacting standards and superior product integrity that legacy systems struggle to match, further positioning themselves at the forefront of manufacturing excellence.
High-Precision Equipment Features
These tools wield adaptive bending technology, ensuring consistency across complex bends and intricate shapes with each use.
Since their inception, improvements like fiber laser sources and automatic process control have revolutionized cutting precision, reducing production errors and enhancing quality.
Moreover, the integration of real-time monitoring systems allow for immediate corrective actions, ensuring that products meet stringent tolerance specifications with minimal deviations.
Advanced software interfaces work in synergy with precision machinery, enabling streamlined workflow, predictive maintenance, and detailed reporting that drives operational efficiency.
This equipment is pivotal in achieving the ultra-fine cuts and detailed edge quality demanded in today’s competitive fabrication markets.
Quality Assurance through Tech
Enhanced technology in press brakes, lasers, and plasmas offer real-time data collection that facilitates immediate quality checks and adjustments. This minimizes the occurrence of defects, upholding a higher standard of output quality.
Technological advancements have elevated on-machine verification capabilities to new heights, ensuring unparalleled precision.
Integrated sensors and analytical tools now empower operators to detect and address potential discrepancies in material properties or machine performance before they escalate into costly errors. This preemptive approach is critical in maintaining an unyielding commitment to quality.
The evolution of industrial equipment paired with sophisticated data analytics has inaugurated an era of predictive quality assurance. This proactive methodology is twofold: it insists on impeccable product consistency while optimizing the production cycle, and it supports a culture of continuous improvement—ensuring that fabrication processes remain resilient and adaptive to evolving industry demands. With smart systems, the margin of "good enough" is supplanted by an insistent pursuit of excellence.
Leveraging Data for Efficiency
The integration of advanced monitoring systems in modern Press Brakes, Lasers, and Plasma machines materializes as a drastic boost in operational efficiency. Real-time data acquisition and analysis facilitate the fine-tuning of processes, leading to a substantial reduction in cycle times and material waste. Such precision, afforded by these technological updates, serves to enhance profitability through improved throughput and resource management.
In embracing the cutting-edge capabilities of data-enhanced machinery, manufacturers gain a formidable edge—a "data-driven compass". This enables them to navigate the complexities of production with an informed perspective, reducing the incidence of downtime and enabling predictive maintenance strategies. As they collect and analyze data, machine operators can anticipate and rectify potential issues, ensuring that equipment performs at peak levels and sustains an uninterrupted production flow.
Real-Time Data Analysis
Real-time data analysis signifies an epochal shift in manufacturing dynamics, fostering informed decision-making.
Advanced analytics allow for a microscopic examination of machine behavior, unveiling inefficiencies with precision once thought unattainable.
Adopting such systems, fabricators and assemblers can track performance metrics continuously, identifying deviations from optimum efficiency immediately.
This immediate feedback loop enables corrective actions to be implemented without delay, therefore minimizing downtime and augmenting output.
The transformation from reactive to predictive operations is a hallmark of manufacturing's evolution.
Predictive Maintenance Insights
Predictive maintenance transcends traditional reactive approaches, leveraging foresight to preempt technical failures.
Employing advanced analytics and machine learning algorithms within industrial machinery such as press brakes, lasers, and plasmas, allows for the discernment of patterns indicative of wear and tear. This intelligence enables operators to schedule maintenance proactively rather than reactively, ensuring machinery sustains optimal performance. By interpreting signs of imminent issues before they escalate, downtimes are significantly reduced, bolstering productivity and dependability.
In parallel, sensors integrated into modern equipment furnish a stream of data rich in implications for the health of machinery. When this data is analyzed, subtle anomalies that may signify the incipient stages of mechanical degradation become detectable. Thus, these insights can be leveraged to mitigate risks proactively, refining maintenance schedules to align with the actual conditions of the equipment rather than relying on predetermined intervals.
Finally, the synthesis of this data into actionable intelligence necessitates a robust framework for data management and analysis. The deployment of sophisticated data capture and analysis tools offers a comprehensive view of the machine's operation, unveiling opportunities not only for maintenance optimization but also for energy savings and process improvements. Such enhancements result in an end-to-end efficiency that directly impacts the bottom line, establishing a competitive edge in a market where uptime is intimately linked to customer satisfaction and business success.
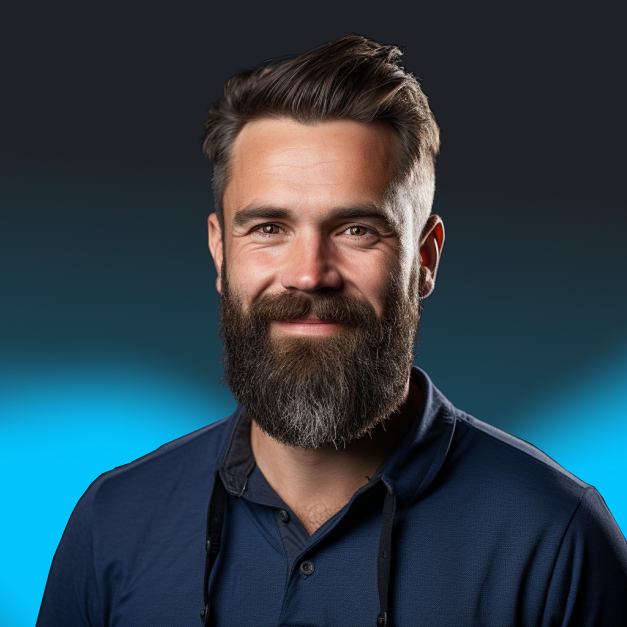
Richard Mason
By day I help people solve problems, by night I'm enjoying IPAs! For fun I work in my garage building gadgets that cost way more than they are worth.