In manufacturing we see that it is constantly evolving and adapting to new technologies and innovative practices. One such revolution lies in the transformative power of Interactive Work Instructions (IWI). These seemingly simple inventions are fundamentally transforming how tasks are approached, managed, and executed on the shop floor, effectively turning human workers into digital counterparts. By augmenting the workforce with digital tools, we are enabling a holistic shift, from a largely analog operational framework to a digitally driven one that carries vast potential for enhanced productivity and growth.
Ever wondered how you could adequately transmit that intricate assembly procedure in a way that leaves no room for interpretation errors? Interactive Work Instructions could be the answer you’ve been in search for.
Beyond Communication: Unleashing the Potential of Interactive Work Instructions
Interactive Work Instructions are not just a mere method of communication. Rather, they serve a much broader purpose, actively acting as a platform which guarantees the uniform approach and consistent execution of tasks within an organization. They represent a unique tangent for manufacturers to adopt digitalization and leverage it within their day-to-day processes. Scout Systems, a pioneer in this arena, affirms the potential behind workforce digitalization through their dynamic solution which centers around Interactive Work Instructions. By enabling users to integrate videos, animations and comprehensive step-by-step guidelines into their instructions, Scout allows workers to gain a rapid grasp on their tasks and proceed with impeccable precision, further solidifying the emphasis on digital transformation.
From Theory to Practice: The Versatility of Manufacturing Work Instructions
Scout System’s platform is built with unmatched adaptability, making it an ideal solution for a wide range of manufacturing environments. Its flexibility ensures seamless integration across processes, from manual assembly to fabrication and quality inspection.
This versatility empowers manufacturers to tackle diverse challenges with precision and consistency. For instance, many users have leveraged the platform to improve their First Pass Yield (FPY), achieving measurable benefits. One example saw defects drop by 50% within the first year of implementation, followed by an impressive 70% reduction in the second year and a 90% reduction by the third year. These results highlight the platform's ability to drive continuous improvement and elevate quality control efforts across industries.
Maximizing Task Execution with Operator Work Instructions
Scout Systems takes the lead again with their implementation of advanced technology in creating operator work instructions. With this tool, floor workers can gain access to detailed and visually enriched work instructions. This level of empowerment guarantees a high degree of precision and efficiency in executing tasks - reducing downtime, waste levels, and driving an overall enhancement in productivity.
Revamping Assembly Line Procedures with Digital Instructions
Alluding to the idea of analog-to-digital workforce transformation, Scout Systems takes it a step further by digitalizing assembly line instructions. This modern approach brings about immense consistency and precision to production processes. By hammering down the communication barriers between design and assembly teams, Scout ensures the resulting product accurately reflects the as-designed intent with greater convergence than ever before.
Re-engineering Manual Assembly through the Lens of Interactive Instructions
When we speak specifically of manual assembly, interactive work instructions revolutionize the craft entirely by transforming analog human workers into their digital counterparts. These instructions provide an accurate real-time map of operator tasks, standardizing processes and enhancing quality. Digital transformation in this regard opens up untapped communication and automation pathways, pushing the boundaries of an otherwise conventional factory's capabilities.
Exploiting Advanced Communication and Automation Capabilities
Beyond the call of basic instructions, these innovative and interactive work instructions hold the capability to collect and analyze real-time data. An early adopter of Scout Systems reported the ability to capture all production data from day one of implementation. This paved the way for automated manual time studies, extensively reducing the need for human intervention. These unlocked potentials for communication and automation can lead to streamlined, efficient, and ultimately more profitable manufacturing processes.
Turbocharging Factory Capabilities via Standardization
Standardization has always been a widely acknowledged strategy when it comes to improving quality. Interactive work instructions, however, redefine standardization by offering a pathway for manifold improvements within a manufacturing setup. These improvements don’t merely enhance the factory's performance; they also facilitate the adoption of lean manufacturing principles, charting a course towards increased efficiency and cost-effectiveness.
Embarking on Your Journey to a Streamlined Manufacturing Ecosystem
Eager to rebuild your manufacturing processes with a digital-first approach? Gear up for an exciting journey towards an optimally streamlined operational ecosystem with Scout’s Free Work Instruction Software. To understand how Scout Systems can help unlock the full potential of Manufacturing 4.0 for your enterprise, consider signing up for their unique Accelerator Program. Take the leap today and re-imagine your manufacturing potential.
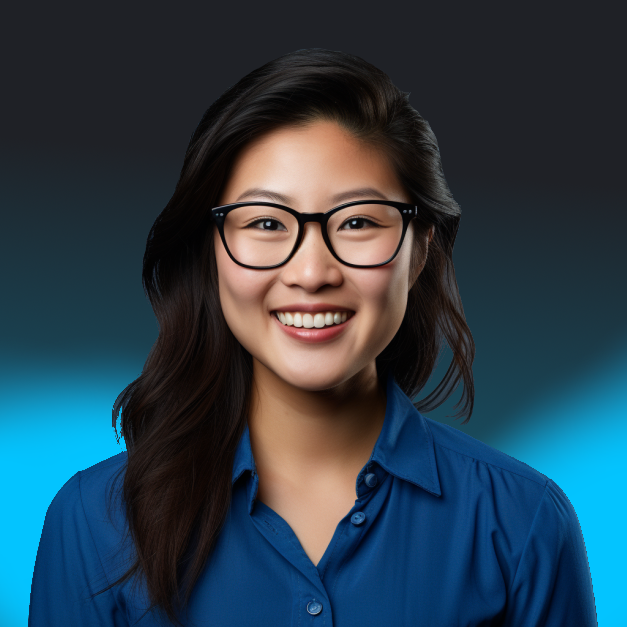
Jen Moore
I absolutely LOVE being outside. Being a soccer enthusiast and a dog mom, I spend much of my free time running with my pups or kicking a ball with my team.