The continuous challenge in finding skilled labor, and increasingly difficultly in maintaining compliance and quality expectations has led to an increase in the use of Standard Operating Procedures (SOP). Traditionally processes have relied on software such as Excel/Word for documentation, however modern SOP software has made those platforms obsolete. The major benefit of using SOP software is that it is exclusive software made to solve the needs of Manufacturers, not a generic tool that is used for every industry.
Why Use Standard Operating Procedures
Let us begin by answering the immediate ‘What's & Whys’. If you are not aware of what standard operating procedures are, in less official terms they are just work instructions. They are used to streamline training by detailing the manufacturing processes of an organization. Traditionally these are printed on paper, and either stored in a binder or hung at the production cell. Manufacturers utilize SOPs to facility onboarding of new employees, as well as to improve their efficiency by providing operators access to tribal knowledge.
SOPs provide greater opportunities for collaboration and analytics, since Manufacturing and Quality Engineers can review/visualize an exact process instead of relying on interrupting Operators and asking them directly how they perform a specific task. Larger customers often expect a Control Plan from their OEMs and within that plan are the SOPs.
Advancements of SOP Software
Before the advent of modern SOP software, Manufacturers relied on Excel, Word, or PowerPoint to create work instructions. While these tools were adequate for their time, they fall short when compared to the capabilities of today’s SOP software. Modern SOP software systems offer a massive advantage by transforming standard operating procedures into dynamic, multi-layered tools. These systems are not just digital versions of instructions; they are comprehensive platforms for data collection and analysis, content creation, and change management.
Modern SOP software integrates powerful analytics tools that enable real-time data collection and performance tracking. This allows manufacturers to gain insights into their processes, identify inefficiencies, and make data-driven decisions for continuous improvement.
Additionally, these systems streamline content creation with intuitive interfaces and collaborative features. Teams can easily create, update, and share SOPs, ensuring that all stakeholders are on the same page. The review and approval processes are also enhanced, offering greater control over changes and ensuring that all updates are thoroughly vetted before implementation.
Tool and Machine Integration
In recent years, the Industrial Internet of Things (IIoT) has emerged as a buzzword, claiming to be the future of Manufacturing. This technology envisions an interconnected factory where data flows seamlessly between devices. When combined with modern SOP software, factories can integrate tools and machinery directly into their work instructions. This integration enables automatic quality checkpoints, where tools communicate results to the instructions in real-time, allowing or disallowing the process to continue based on the data received.
Manufacturers that embrace both IIoT and modern SOP software can achieve automated quality checks, leading to higher product quality with reduced labor. Preventative maintenance schedules can dynamically adjust based on actual usage, minimizing machine drift and extending equipment life. By integrating SOP software with ERP systems, paperwork is reduced, and job statuses are updated automatically. Each of these improvements enhances factory efficiency and quality, all while lowering costs by reducing the reliance on human labor.
Data Collection and Analytics
Another major benefit of utilizing modern SOP software is the ability to capture and process production data. As operators engage with digital work instructions, they effectively become sensors, providing engineers with exceptionally accurate measurements of value-added and non-value-added labor. This eliminates the need for traditional cycle time studies, as every production run is automatically measured and analyzed.
The data collected through SOP software is far more powerful than simply knowing cycle times; it’s the accessibility and integration of this data that unlocks its true potential. SOP software systems can be interconnected via Application Programming Interfaces (APIs), seamlessly exchanging vital information. This integration significantly reduces paperwork and manual data entry, further decreasing labor costs while eliminating human error.
Manufacturers that implement SOP software gain access to new forms of automation that are impossible for those relying on analog methods. This advancement leads to greater efficiency, accuracy, and overall productivity in the manufacturing process.
Your ERP is seamlessly connected with your SOP software through APIs, automatically deploying the production schedule to all production cells. As Operators sign into their portal, they receive their tools and materials list, along with operational guidelines to prepare for the production order. During the workflow, digital work instructions communicate with smart tools, enabling or disabling them depending on the task and dictating the appropriate torque values. Inputs such as torque values, test equipment results, and machine usage are automatically collected by the platform and checked to ensure high quality.
Cameras mounted above the production cells capture images at critical stages of the process, which are then linked to the serial number of the product being built, providing you with unparalleled product traceability. Any complications are immediately broadcast to support staff, informing them of the problem and its location. Upon completion of the production order, the SOP software closes out the job in the ERP and compares the production run's data to historical records to identify anomalies. If discrepancies are found, the system notifies the Quality department and requests a review.
With a detailed understanding of the production process, Manufacturing Engineers can review standard procedures to identify opportunities for boosting efficiency and quality even further.
Expected Return on Investment
When calculating the return on investment (ROI) for purchasing an SOP software system, it’s crucial to compare it against your current analog expenses. Paper-based processes are inherently costly: expenses include printers, paper, ink, and the labor associated with deploying and collecting documents, recording data, data entry, and managing revisions. Additionally, there's the cost of collecting cycle time data and the risks associated with inaccurate data. These challenges are prevalent in most factories, making the transition to digital SOP software a financially sound decision. When you factor in the new forms of automation that digital SOP software enables, the potential for increased efficiency and cost savings becomes even more compelling.
Scout Systems' offers free work instruction software, charging only when a Manufacturer wants to deploy the digital work instruction portal used at the Operator level. Even at the paid level, most Manufacturers can recover the cost of the platform within days. For those that are looking to rapidly deploy the technology using the most advanced features, we recommend the Accelerator Program - a 90 day blitz with a money back guarantee.
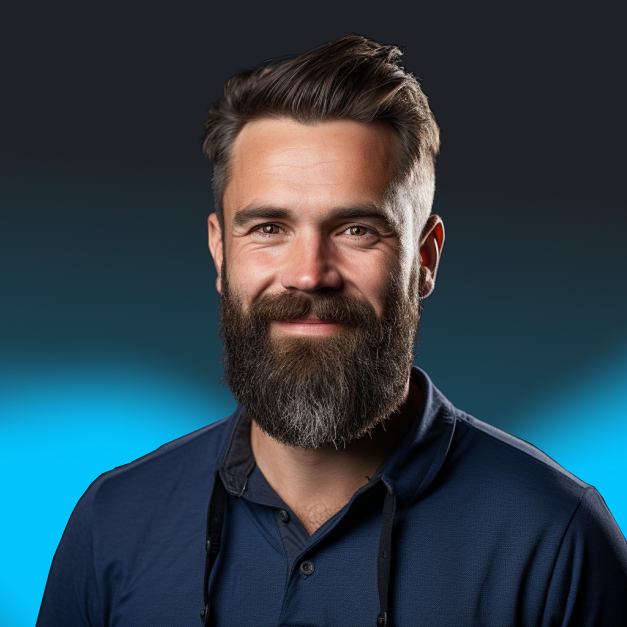
Richard Mason
By day I help people solve problems, by night I'm enjoying IPAs! For fun I work in my garage building gadgets that cost way more than they are worth.