In modern manufacturing cells, numerous tools are calibrated to specific torque values to ensure precision. Lean Manufacturing practices often use color coding to help operators avoid selecting the wrong tool. However, many of these tools rely on internal clutch systems for setting torques, which can be unreliable due to varying material properties and heavy usage. The next advancement in this field is the implementation of smart tools. These innovative tools feature built-in technology that automatically adjusts torque values, thereby reducing the number of tools required. Equipped with sensors to measure the realized torque value, smart tools ensure the desired torque is consistently achieved. This evolution represents a significant enhancement in tool capability, although it still depends on operators to select the appropriate tool settings.
Smart Tool Integration System
While smart tools offer remarkable benefits, their true potential is realized when integrated seamlessly into your process workflow to ensure consistent torque values. Without proper integration, there is a risk of errors. Additionally, traditional systems often require manual data downloads from each tool or controller to analyze production tool data. By pairing smart tools with Work Instruction Software, which guides operators through each step, smart tools can receive notifications about their position in the process and ensure the correct torque is applied. This connectivity represents a significant breakthrough in manufacturing automation, paving the way for enhanced efficiency and accuracy.
A New Era of Scout Systems
After months of collaboration with customers and smart tool vendors, Scout Systems is excited to announce that we be rolling out Smart Tool Integration in our Work Instruction Software in 2024. Known for our incredible ease of use and vast system offering, expanding to include Smart Tool Integration is yet another way we can provide manufacturers a single platform designed for scalability and full optimization of a factory.
Our platform will communicate seamlessly with smart tools on the production line, putting tools to sleep during unnecessary process steps, waking them when needed, selecting the appropriate torque values, and verifying that the correct torques are achieved. Coupled with our Unit Identifier feature, manufacturers will be able to access specific product data and confidently review the results of each rundown. This integration represents a significant step forward in manufacturing efficiency and precision.
Technical Aspects of Smart Tool Integration
The primary goal of adding Smart Tool Integration to the Scout Systems' platform, beyond tool control and result recording, was to simplify tool management for manufacturers. Leveraging the Service Application, already installed on all Compass stations for data encryption and Serial Communication, we have extended its capabilities to communicate over the local network using TCP/IP. Manufacturers only need to connect the smart tool to the same network where Compass is running. Once the tool is configured and connected, our platform will be able to communicate with it immediately, streamlining the integration process and enhancing operational efficiency.
Within HQ Designer, users will have the ability to designate a step to utilize a smart tool. They can specify the desired MID (torque value), set the total number of rundowns for the step, and choose whether the instruction will AUTO-NEXT to the subsequent work instruction step. Additional details and features will be unveiled in the near future, providing even more robust capabilities for smart tool integration.
Prepare for the Future
Work Instruction Software serves as a gateway to both standardization and the latest manufacturing technologies. It reduces the cost of quality by automating quality checks and eliminating the need for labor-intensive data collection. Training time for new employees is drastically reduced, and revision control becomes effortless. The benefits continue to grow, making it clear that replacing legacy systems with Scout Systems is the best way to prepare for the future.
If costs are a concern, you can start with our Free Work Instruction Software today, enabling your staff to create work instructions more quickly and with higher quality. When you're ready to fully digitize your factory, transitioning will be as simple as flipping a switch.
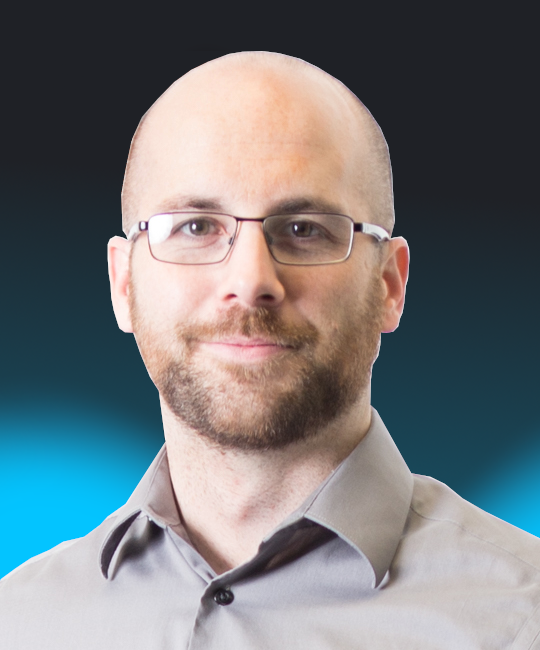
Ben Marsh
I've spent my career in Manufacturing, and can't stop trying to make things more efficient. At home, I am a master Lego builder with my son.