Unearth the potential of control plans for manufacturers to streamline operations, enhance product quality, and outshine competitors.
Understanding Control Plans
Control plans define the rules for monitoring and managing certain operational variables that significantly impact the product quality. By delineating robust guidelines, these documents help control and maintain manufacturing processes in optimal conditions.
A control plan is a tool that illustrates what measures a business should take during its manufacturing process to maintain control and ensure quality. By providing a standardized and structured approach to quality control, it enhances operational consistency and effectiveness.
What is a Control Plan?
A Control Plan is a methodical and comprehensive approach designed to monitor, control, and manage the processes and outcomes in manufacturing. It's a roadmap that orchestrates the sequential steps manufacturers must follow to ensure product quality and prevent defects.
A Control Plan acts as a dynamic toolkit, bolstering performance, quality, and consistency by directing precise control points and outlining corrective measures in the manufacturing process.
This pivotal tool streamlines the process by pinpointing the critical points where controls must be implemented. It underlines what to control, how to control, and who is responsible for the control, ensuring each part meets the precise specifications.
Plunging deeper, a Control Plan also includes monitoring methods, measurement systems, and outlines corrective actions if the specifications are deviated. It's not just a tool, it's a dynamic toolkit bolstering performance, quality, and consistency in the manufacturing process.
Importance of Control Plans in Manufacturing
Control Plans revolutionize manufacturing by fundamentally altering workflow, ensuring there is a proactive strategy in place to maintain quality and efficiency. Their strategic integration is a game changer, mitigating risks and averting process deviations before they occur.
Control Plans hold an intrinsic role within the manufacturing ecosystem. They are the lifeline that enables manufacturers to optimize operations, ensuring every product meets the defined standards and regulatory requirements.
A well-implemented Control Plan plays a crucial role in giving manufacturers a competitive edge. It ensures a high level of consistency and reliability, translating into satisfied customers and brand loyalty, aspects vital to business success in a competitive market.
Types of Control Plans
Navigating the diverse world of control plans is vital due to its purpose-built nature. Static, dynamic, and centralized control plans each have distinct objectives and applications in manufacturing.
A static control plan, often used for processes with a fixed sequence, harnesses consistent standards to ensure product quality.
On the other hand, dynamic control plans offer flexibility, adjusting to process changes and variations, for continuous improvement within complex manufacturing scenarios.
Centralized control plans stand out with a comprehensive approach, overseeing multiple processes or sites, underscoring their significance to large-scale, integrated manufacturing operations.
Components of a Control Plan
Every control plan consists of several crucial components, creating a structured roadmap for manufacturing processes. These integral pieces include process description, characteristics measurements, control methods, and disposition for out of control condition.
A closer inspection of a control plan reveals key elements. The operational steps to be controlled, corresponding process measurements, control methods to monitor performance, and specific actions for deviation scenarios form the backbone of effective control plans.
Creating an Effective Control Plan
Crafting an effective control plan hinges on precise identification of critical control points, definition of control limits, and diligent implementation of proper monitoring and measuring systems. It also entails a delineation of coherent corrective actions to ensure regulatory compliance and sustain production quality.
Delving into the components of a successful Control Plan, one dives deep into multiple facets. Detailed attention to training and education, comprehensive documentation, and regular communication, along with steadfast auditing and review, empowers an assembly line with the power of a finely tuned Control Plan.
Identifying Critical Control Points
The journey to successful manufacturing commences with identifying key control points. These unseen heroes ensure consistent product quality, preventing unfavorable scenarios from surfacing during production cycles.
Critical checkpoints within your control plan function as a blueprint for quality management. They mark areas requiring heightened vigilance, as potential pitfalls or opportunities for improvement.
Mastering the identification of these critical points demands a blend of comprehensive risk analyses, and an intimate understanding of your production processes.
Crucial touchpoints where errors could occur must be marked out and monitored. These breakpoints, if unchecked, could severely compromise overall product quality and efficiency.
In essence, the art of pinpointing critical checkpoints in a control plan is a constructive path to iron out potential defects, conserve resources and ensure customer satisfaction. It's the fine line separating average from exceptional in the manufacturing realm.
Establishing Control Limits
Control limits form the trifecta of a control plan's framework in manufacturing, alongside process inputs and outputs. Their primary function is to signify the point of principle performance variation, thereby initiating corrective measures.
The role of control limits is vital in sustaining operational excellence. Defined upper and lower thresholds signify if a process has deviated from its normal functioning, drawing attention to underlying issues.
Discerning the crux of control limits is fundamental for manufacturers who seek consistent product quality. Adequate setting of these thresholds aids in mitigating costly blunders and product failures.
Control limits bear significant collaboration with process variation and quality control. Regular assessment of these established parameters forms an integral part of ensuring process stability and excellence.
Control limits in a control plan also enhance proactive disaster management. Bundled with swift corrective measures, they curtail material wastage, reduceed downtime, and bolster overall productivity, thus propelling customer satisfaction and innovation.
Implementing Monitoring and Measuring Systems
Leveraging monitoring systems can significantly enhance the efficiency of a control plan. These systems aid in identifying deviations from the established standards, facilitating quick corrective measures.
Monitoring systems not only highlight discrepancies, but they also generate valuable data to evaluate overall operation efficiency. This insight aids in refining tailor-made strategies enhancing control plan efficacy.
Incorporating measuring systems within a control plan is equally vital. They deliver a quantitative understanding of performance, helping identify problematic areas and potential areas of improvement.
An integrated approach of both monitoring and measuring systems drives a robust control plan. The combination ensures efficiency, builds quality assurance, and contributes to better customer satisfaction.
Defining Corrective Actions
Corrective actions serve as the lifeline of a control plan; a robust plan requires well-structured actions to rectify deviations timely and efficiently. These actions not only fix immediate problems but also prevent their recurrence, hence enhancing overall process stability.
Understanding the role of corrective actions in streamlining control plans is central to ensuring product quality and consistency. By identifying the cause of deviations and implementing appropriate measures, manufacturers can seamlessly optimize their operations and fulfill customer expectations with ease.
Implementing Control Plans in Manufacturing
Technological innovations are accelerating the implementation of control plans in manufacturing. Digital platforms, automation, and data analytics are reshaping the way control plan processes are executed, augmenting operational efficiency.
Transitioning to a control plan-embedded manufacturing process demands an intelligent approach. It begins with conducting a comprehensive process risk assessment, followed by defining key control points, setting control limits and establishing robust monitoring systems. Crucial too is the provision of high-quality training to team members, underpinning the successful integration of this plan.
Training and Education
To ensure effective implementation, integrate control plan training for manufacturing excellence. An intersection of education and control plan implementation will create an environment conducive to heightened productivity.
- Plan focused training sessions that prioritize critical aspects of control plan implementation.
- Ensure access to resources, online courses, and workshops that further enhance understanding.
- Involve industry experts to deliver insightful sessions or seminars.
- Incorporate regular follow-up sessions to reinforce training materials.
Documentation and Communication
For successful Control Plan execution, clean documentation and effective communication are non-negotiable. Documentation ensures transparency, and communication enables rapid response to changes and deviations.
- Robust documentation provides a clear roadmap of control measures, control points, roles, and responsibilities.
- Documenting changes in control processes makes auditing a breeze and helps track the plan’s efficiency.
- Effective communication facilitates faster decision-making, reducing delays in control plan adjustments.
- Regular communication helps to keep all stakeholders informed, promoting collaboration.
Auditing and Review
To perform at the highest level and stay relevant in a highly competitive field, the process of regular auditing and reviewing is crucial to the effectiveness of your control plans. Periodic reviewing allows for the identification and implementation of necessary changes, ensuring your control plan remains a powerful strategic tool.
- Evaluating the effectiveness of current controls
- Identifying areas that require improvement
- Monitoring adherence to control limits
- Review for timely updates in process or standards
- Update training and communication strategies
- Assessing the suitability of corrective actions taken
- Ensuring compliance with internal and external regulations
- Prioritizing future investments in innovation and technology
Benefits of Mastering Control Plans
Mastering Control Plans positions manufacturers at the cutting edge of a swiftly transforming manufacturing landscape. It engenders continuous improvement, risk mitigation, and enhanced predictability; factors pivotal in delivering superior customer value.
Indubitably, an optimized Control Plan is the main driver of manufacturing success. It enables efficient allocation of resources, ensures process consistency, strengthens customer trust, and carves a niche in an increasingly competitive market.
Improved Quality and Consistency
Mastering control plans inherently fosters improved quality and consistency. This dynamic duo is attained by making critical control points effortlessly manageable, thereby minimizing variability and disparity in the final product.
- Identifying critical points that directly influence product quality.
- Establishing rigorous control limits to prevent defects.
- Implementing robust monitoring systems to ensure consistent adherence to set parameters.
- Defining effective corrective actions to rectify deviations, fostering consistency.
- Periodic training of staff to upskill them in maintaining quality consistency.
- Documenting all processes and controls for transparency and uniformity.
- Regular auditing and reviews to verify adherence to quality standards.
Increased Efficiency and Productivity
In the manufacturing realm, control plans serve as a pivotal catalyst escalating both efficiency and productivity. This elevation manifests when all key elements of production align harmoniously, achieving targeted objectives effectively.
A well-executed control plan streamlines processes, eliminating extraneous steps and maximizing resources. As a result, operations gain momentum, yielding higher output within shorter time frames.
Efficiency also receives an upward thrust when managerial oversight is robust. Control plans, by their very nature, mandate heightened vigilance over every production phase, inevitably leading to a more efficient workflow.
Productivity gains stem from this same rigorous scrutiny. When hitches are detected and resolved promptly, downtime is minimized. Swift, consistent production becomes the norm, amplifying overall productivity.
Lastly, by predictably delivering a superior product, manufacturers cement their reputation for reliability and quality. This boosts worker morale, driving productivity. Consequently, control plans become indispensable tools for any manufacturer intent on boosting efficiency and productivity.
Customer Satisfaction and Retention
Efficient control plans are the keys to unlocking customer satisfaction and retention. These tools elegantly handle product quality, ensuring a consistent experience delighting customers.
Reducing product recalls and rejections, an efficient control plan lowers frustration rates. This assures customers that their chosen manufacturer values quality, leading to greater trust and loyalty.
Control plans serve as the invisible hand, subtly directing operations to impress customers with reliability. Built on quality and consistency, it forms the backbone of a product’s reputation.
In the competitive world of manufacturing, efficient control plans shine. Demonstrating a commitment to high standards reassures customers, increasing satisfaction and retention, aiding manufacturers in standing out.
Competitive Advantage and Innovation
Winning the competitive game requires innovative strategies. Control plans, often overlooked, serve as pioneering tools to prompt competitiveness by fostering invariable quality and manufacturing efficiency.
Control plans are integral for unlocking innovation, fostering a proactive approach to problem-solving. They not only enhance operational excellence but also secure a hard-to-achieve competitive advantage.
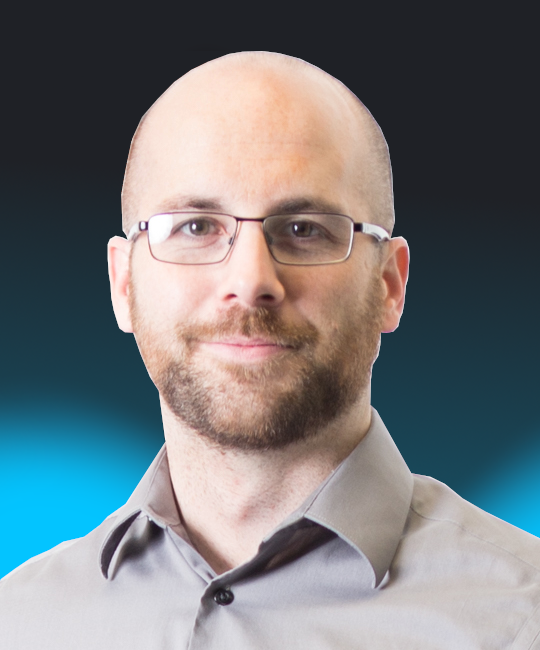
Ben Marsh
I've spent my career in Manufacturing, and can't stop trying to make things more efficient. At home, I am a master Lego builder with my son.