In the realm of industrial manufacturing, precision is crucial, and any deviation can lead to substantial financial losses and reduced product quality. The problem lies in the inherent complexity and variability of production processes, which demand meticulous control and constant adjustments.
Enter Advanced Process Control (APC), the strategic linchpin in modern manufacturing.
Equipped with APC, assemblers and fabricators can leapfrog traditional methods, achieving unparalleled consistency and efficiency within their processes. This results in not only impressing customers but leading the charge in innovation.
Pillars of Advanced Process Control
At the heart of Advanced Process Control (APC) lie robust models and algorithms that allow for predictive and adaptive process adjustments. These foundational elements are crucial for the accurate forecasting of process behaviors, enabling proactive control strategies that mitigate potential disruptions and maintain optimal performance. Mastery of these components ensures that assemblers and fabricators can reliably navigate the complex landscape of modern manufacturing processes.
In strengthening the framework of APC, there's an imperative to integrate systems that encompass real-time data acquisition and process visualization. These systems must work in concert to form a "closed-loop control" environment where data is not merely collected but is also analyzed and acted upon in a timely and effective manner. The synergy of these technologies, when finely tuned, empowers fabricators to exert precise control over their manufacturing operations, thereby enhancing quality outcomes and operational efficiency.
Fundamental Concepts Defined
Advanced Process Control (APC) hinges on seamlessly integrating feedback mechanisms, predictive analytics, and adaptive systems within manufacturing processes. This integration optimizes operations, delivering consistent quality and reducing variability.
At its core, APC involves orchestrating various control methodologies to fine-tune manufacturing processes. Robust statistical models and automation technologies replace traditional manual adjustments, augmenting precision and adaptability.
Fact: Early adoption of APC can increase production efficiency by up to 15%, transforming manufacturing performance.
Understanding and implementing APC concepts allows for continual process enhancements. By analyzing real-time data and employing predictive control strategies (e.g., model predictive control), assemblers can dynamically adjust to process variations, achieving superior product integrity and operational excellence.
Core Benefits to Operations
Implementing Advanced Process Control (APC) significantly escalates production caliber and throughput.
- Enhanced Quality Control: APC sustains product excellence through real-time adjustments and consistent standards.
- Increased Throughput: Optimization of processes results in higher production rates without compromising quality.
- Reduction in Production Costs: Efficient use of resources and minimization of waste translates to substantial cost savings.
- Extended Equipment Life: Proactive maintenance and optimized operations reduce wear and tear on machinery.
- Improved Safety: Automation minimizes human error, enhancing workplace safety and compliance.
- Scalability: APC allows for seamless integration of new technologies and scaling up of production as demand grows.
Assemblers can witness a marked reduction in process variability with APC implementation.
By mastering APC, operations become more predictable, resilient, and aligned with market expectations.
Technologies Empowering APC
Advanced Process Control (APC) is revolutionized by contemporary technological advances.
- Model Predictive Control (MPC): Utilizes mathematical models to predict future process behavior and optimize control actions.
- Real-Time Optimization (RTO): Adjusts process operation in real-time for maximal efficiency and profitability.
- Artificial Intelligence (AI) and Machine Learning (ML): Employs algorithms to adaptively learn from data and improve process control.
- Cyber-Physical Systems (CPS): Integrates computation, networking, and physical processes for enhanced monitoring and control.
- Digital Twins: Creates virtual copies of physical systems for simulation and analysis to predict performance and optimize operations.
- Industrial Internet of Things (IIoT): Connects machinery and devices for improved data collection and autonomous control.
- Advanced Analytics: Analyzes complex datasets to gain insights and foresight into process behaviors and potential optimizations.
These tools form the vanguard in APC, introducing unmatched precision and adaptability.
Leveraging these technologies, APC transforms into a dynamic, intelligence-driven pillar of modern manufacturing.
Designing APC Strategies
When charting the course of APC strategies, it is crucial to delineate clear objectives and performance indicators that align with overarching business goals. This entails conducting thorough process analyses, identifying critical variables, and shaping robust control architectures that can withstand the ebbs and flows of production demands. A comprehensive strategy not only embraces current technological capabilities but also allows for scalability and integration of future advancements in process control.
The development of an APC strategy requires rigorous assessment of the control loop structure, ensuring that each element—from sensors to actuators—performs optimally within the system. Consideration of stochastic variables and the application of predictive models will enhance the system's responsiveness and stability. Incorporating feedback from real-time analytics and AI-driven insights can precipitate a bespoke response mechanism. The ultimate aim is to achieve a confluence of precision, efficiency, and resilience that ensures consistent quality output and elevates the competitive standing of the operation.
Blueprinting Control Architecture
Blueprinting control architecture is the strategic design of an integrated control system tailored to the specific needs of a production process.
- Evaluate Existing Systems: Analyze the current state of process control systems to identify strengths and areas for improvement.
- Define Objectives: Clearly articulate the performance targets and criteria for the advanced process control (APC) system.
- Select Control Strategies: Choose the appropriate control methodologies and algorithms that align with the defined objectives.
- Design Hierarchical Structure: Establish a scalable multi-layered control architecture, where high-level strategic decisions guide lower-level operational controls.
- Integrate Components: Ensure seamless interaction between all the elements of the control system, from sensors and actuators to controllers and user interfaces.
- Plan for Scalability and Flexibility: Make provisions for future expansion and adaptability to new technologies or process changes.
- Develop Communication Protocols: Create robust data exchange pathways to facilitate information flow among components.
A meticulous approach to component integration is vital for a responsive and efficient control system.
Through the fusion of these elements, we construct a resilient control architecture that advances operational excellence and fosters innovation.
Ensuring System Scalability
Scalability is a cornerstone in contemporary process control systems. It ensures that these systems can adapt and expand in response to evolving production demands without compromising performance or requiring extensive reconfiguration.
Advanced process control systems must be designed with scalability in mind. This includes using modular components that can be easily upgraded or replaced, and software that can accommodate increased loads or changes in process complexity. Such foresight reduces future costs and downtime associated with expanding or updating the system.
Importantly, scalability also extends to data management and analytics capabilities. As processes grow, the volume of data generated increases exponentially. Process control systems equipped with scalable data structures and storage solutions can manage this growth without loss of efficiency or speed.
By prioritizing scalability at every stage of control system design, we ensure long-term sustainability and readiness to integrate emerging technologies. This foresight empowers businesses to maintain a competitive edge and meet the dynamic challenges of their respective industries, while ensuring a smooth transition during phases of expansion or technological overhaul.
Implementing APC Solutions
System architecture and network infrastructure play pivotal roles in deploying advanced process control (APC) solutions, ensuring seamless integration and reliable performance.
To actualize APC, it is essential to establish robust communication protocols and server platforms that can accommodate real-time data processing and control algorithm execution, thereby enabling precise and adaptive process management.
Integration of APC necessitates a careful examination of existing workflow configurations and process optimization objectives, to ensure that solutions align with a facility's unique operational requirements.
Step-by-Step Integration Process
The initial step involves a meticulous audit of current system capabilities, pinpointing both strengths to leverage and deficiencies to address. This groundwork is crucial for successful APC integration and subsequent operation.
Next, a detailed integration plan should be meticulously crafted, incorporating an analysis of the process landscape, identifying the optimal nodes for sensor and control unit installation, and establishing data flow pathways. Critical to this stage is ensuring that all elements adhere to industry standards and explicitly detailing the sequence for implementing the APC system. This blueprint lays the foundation for seamless deployment, mitigating potential integration pitfalls and optimizing the operational transition.
Subsequently, the phased rollout of the APC system commences. This carefully staged approach begins with pilot testing in selected process sectors to refine control strategies and verify system robustness before broad-scale implementation. During this phase, it is imperative to closely monitor performance metrics, recalibrating control parameters to achieve desired outcomes and minimizing process disruptions.
Finally, post-implementation audits must be scheduled to continuously appraise the APC system’s performance, ensuring its sustained efficacy. This appraisal includes rigorous analysis of process control data, identification of any deviation from set performance benchmarks, and determination of areas for further optimization. Continuous improvement through regular review not only upholds production integrity but also paves the way for future advancements in process control technology.
Training for Optimal Use
Proper training is the keystone for harnessing the true potential of advanced process control (APC) systems. Without the right knowledge and skills, even the most advanced systems cannot be fully optimized. Therefore, specialized training programs should be developed, aligned with the specific needs of the APC system in use.
Comprehensive programs are necessary to equip operators with a deep understanding of the APC's principles and functionalities. This training should encompass theory and hands-on exercises that replicate real-world scenarios, promoting a substantial grasp of how the system behaves under different operational conditions. Enabling operators to anticipate and react to process variations ensures that they maintain control efficiency and effectiveness.
Retaining a competent specialist or engaging with the APC vendor for training delivery can be highly advantageous. Such experts not only provide advanced insights into the system's capabilities but can also share best practices for troubleshooting and system optimization. This cultivates a team of well-versed personnel capable of exploiting the full range of the APC system's features.
Moreover, a commitment to ongoing education is critical for continuous process improvement. As technology evolves and new features are introduced, recurrent training updates become necessary to ensure that operators stay current with the latest advancements. This dedication to knowledge expansion not only enhances the capabilities of the operators but also reassures clients that they are receiving the highest quality service from a team that is at the forefront of process control sophistication.
Overcoming Common Implementation Roadblocks
Effective implementation of Advanced Process Control (APC) requires a confluence of precise planning and strategic execution. Any deviation or oversight can lead to implementation delays or even system failure, which can erode trust and frustrate stakeholders.
Integration complexities often arise from existing legacy systems that are entrenched within a facility's fabric. These systems may lack interoperability or the modern interfaces required for seamless APC integration. Such scenarios demand meticulous system analysis, judicious planning, and potentially custom solutions to bridge the compatibility divide. Established protocols and methodologies will assist in mitigating risks associated with system integration, ensuring a smoother transition to advanced control mechanisms.
Moreover, insufficient staff expertise can stifle effective APC deployment. Overcoming this challenge involves not just initial training but the institution of a continuous learning environment. This is accomplished by nurturing an organizational culture that values skill enhancement and provides ongoing opportunities for professional development within the context of APC.
Finally, budgetary constraints can pose significant hurdles in adopting APC technologies. Overcoming fiscal limitations requires a thorough demonstration of the potential Return on Investment (ROI) that APC systems offer. This entails presenting comprehensive analytics showing reduced operational costs, increased efficiency, and enhanced product quality. By substantiating these benefits with verifiable data, it becomes possible to secure the necessary funding and stakeholder buy-in for successful APC implementation.
Measuring APC Success
Effective process control reflects in consistent product quality and throughput optimization, factors crucial for customer satisfaction and operational excellence.
In assessing APC effectiveness, key performance indicators (KPIs) such as reduction in variability, energy savings, and improved safety records serve as tangible benchmarks, illustrating the real-world impact of advanced process control.
Lastly, the transition to "predictive" and "adaptive" modes from "reactive" approaches underscores a profound leap in process capabilities, demonstrating APC's maturity.
Essential Performance Metrics
Optimization of cycle times is fundamental.
To truly grasp APC impact, consider the mean time between failure (MTBF) metric. A hallmark of advanced control systems lies in elevating equipment reliability. Quantifying intervals between breakdowns reflects the robustness of control strategies, and a high MTBF suggests certain stability. Significantly, this is just one aspect of the extensive panorama of APC performance metrics.
Yield maximization remains a primary focus.
Maintaining low rates of defective units is essential—it's a direct reflection of process precision. A minimized defect rate not only signifies superior control but also translates to savings and customer satisfaction. With APC, the target is to meet—if not surpass—industry benchmarks in producing flawless products consistently.
The capability to maintain critical process variables within narrow limits is indicative of APC effectiveness. Developing a solid understanding of process variability and consistency metrics, such as the standard deviation and Cp/Cpk indices, is vital. Continual improvement post-APC implementation through these indicators can advance an assembler’s credibility and customer confidence.
Long-Term Monitoring Techniques
Long-term monitoring forms the backbone of advanced process control (APC) sustainability. To ensure the longevity and reliability of APC systems, persistent observation is paramount.
Over the arc of usage, systematic data collection is a cornerstone of maintaining an optimized operational state. Sophisticated algorithms and robust monitoring tools track process drifts, shifts in efficiency metrics, and predictive maintenance needs. Long-term data serves to refine APC models, ensuring consistent performance over time. It is imperative that these insights be regularly analyzed and utilized to preemptively address potential issues, thus avoiding unplanned downtimes.
Furthermore, deploying continuous improvement frameworks like Six Sigma within APC paradigms helps pinpoint variances. By coupling statistical analysis with real-time monitoring data, adjustments can be made to calibration parameters that fine-tune processes for peak efficiency. The ongoing quest for perfection makes long-term monitoring not just a task, but a strategic imperative.
In conclusion, leveraging deep analytics tools for evaluating long-term trends and patterns establishes an elevated standard of control. This practice not only ensures that APC systems are performing optimally in the present but anticipates and mitigates future performance dips or deviations. Through robust long-term monitoring, manufacturers foster resilient processes that meet and exceed market demands, maintaining a competitive edge in their respective industries.
Continuous Improvement Framework
In the realm of contemporary manufacturing, the continuous improvement framework operates as the cornerstone of relentless pursuit of excellence. It signifies an integral commitment, where the goal is perennial enhancement, not mere compliance.
Continuous improvement is not an event; it's a culture. This philosophy is rooted in iterative progress and persistent refinement.
An effective continuous improvement framework is often predicated on methodologies such as Plan-Do-Check-Act (PDCA) or Define-Measure-Analyze-Improve-Control (DMAIC). These methods foster a disciplined approach to process optimization, emphasizing the importance of meticulous analysis and structured problem-solving.
At the core of this framework, there is a recognition that process control technology must co-evolve with industrial processes. Advanced Process Control (APC) systems are expected to adapt to changes in process dynamics, ever-evolving product specifications, and new material properties. Only through a rigorous continuous improvement protocol can APC systems consistently deliver superior performance, anticipating and neutralizing potential inefficiencies before they crystallize into larger issues.
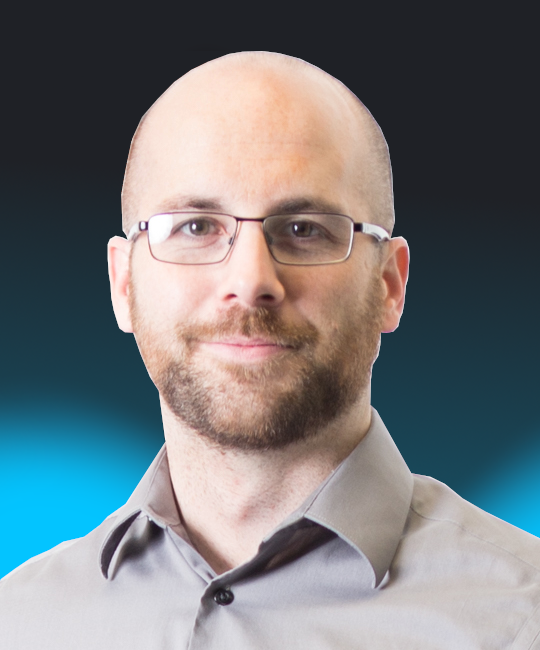
Ben Marsh
I've spent my career in Manufacturing, and can't stop trying to make things more efficient. At home, I am a master Lego builder with my son.