In today's competitive manufacturing landscape, the role of Manufacturing Key Performance Indicators (KPIs) cannot be overstated. These crucial metrics serve as the backbone of efficiency, guiding businesses toward operational excellence and superior productivity. Here, we wanted to explain why Manufacturing KPIs are fundamental in optimizing manufacturing processes and ensuring sustainable growth.
Reading about the nuances of Manufacturing KPIs will make it easy to understand their critical role in distinguishing between value-adding and non-value-adding activities. We'll explore how these indicators not only drive efficiency but also foster a culture of continuous improvement. How they enable businesses to adapt and thrive in an ever-changing market landscape.
Furthermore, we'll navigate through the transformative impact of the Fourth Industrial Revolution on manufacturing. This part will highlight the shift towards digitalization and the integration of advanced technologies. This digital leap, underpinned by Manufacturing KPIs, marks a paradigm shift from traditional practices to a more agile, data-driven approach, significantly enhancing operational capabilities.
Join us as we unravel how Scout Systems facilitates this digital transformation, providing insights into overcoming common digitalization challenges and harnessing the full potential of Manufacturing KPIs through digital systems.
This exploration is not just about metrics; it's about empowering businesses to stay ahead of the curve. It is about leveraging data to make informed decisions and driving operations toward unmatched efficiency and excellence.
Why Manufacturing KPIs are the Backbone of Efficiency
In manufacturing, Key Performance Indicators (KPIs) are crucial. They are data sets that measure a factory's efficiency and value output. Essentially, they differentiate between value-adding activities, which customers pay for, and non-value-adding ones, which signify waste. This distinction is vital. By understanding and reducing waste, factories can enhance efficiency.
KPIs serve as the backbone of manufacturing process efficiency. They provide a clear picture of operational success and areas needing improvement. For instance, consider the basic KPIs of time spent creating value versus waste. By measuring these, factories can pinpoint inefficiencies and streamline processes.
Manufacturing KPIs
Moreover, KPIs evolve with a factory's maturity. Once initial waste is minimized, attention shifts to enhancing the speed and efficiency of value creation. This is where more advanced KPIs, like Overall Equipment Effectiveness (OEE) or Scout Systems' Overall Station Efficiency (OSE), come into play. These metrics consider performance, availability, and quality, offering a holistic view of factory effectiveness.
In essence, KPIs are not just numbers but tools for continuous improvement. They guide factories in making informed decisions, reducing waste, and enhancing productivity. As the manufacturing landscape evolves, especially with the advent of the digital era, KPIs become even more critical. They transform from mere metrics to strategic drivers of digital transformation and operational excellence.
By integrating KPI tracking with digital solutions, factories can achieve unprecedented levels of transparency and efficiency. In turn, this fosters a culture of continuous improvement and operational excellence, ensuring that manufacturing processes remain competitive and future-proof.
The Fourth Industrial Revolution: Transforming Manufacturing with Digitalization
The Fourth Industrial Revolution, often termed Industry 4.0, symbolizes the seismic shift in manufacturing, primarily driven by digitalization. This era ushers in a transformative landscape where digital work instructions and advanced software play pivotal roles, revolutionizing traditional manufacturing processes.
Traditionally, manufacturing relied heavily on manual operations and paper-based instructions, which were not only time-consuming but also prone to human error. This conventional method constrained productivity and flexibility. It hindered manufacturers' ability to respond swiftly to market demands and customization requirements.
Using Digital Work Instructions
However, the advent of digital work instructions has marked a significant departure from these outdated practices. These instructions, delivered through sophisticated software platforms, offer a more dynamic, interactive, and user-friendly approach.
They provide real-time, step-by-step guidance to operators, ensuring precision and consistency across the production line. This digitalization mitigates errors and significantly reduces training time for new employees, enhancing operational efficiency.
Moreover, modern manufacturing processes, underpinned by digitalization, enable real-time monitoring and analytics. This shift allows for predictive maintenance, minimizing downtime, and optimizing production schedules. With traditional methods, insights are often retrospective and based on historical data. Now, digitalization empowers manufacturers with foresight, facilitating proactive decision-making.
In essence, the Fourth Industrial Revolution and its digital underpinnings transform manufacturing into a more agile, efficient, and data-driven domain. The impact of digital work instructions and software is profound. It brings an era of unprecedented precision, customization, and efficiency, starkly contrasting with the limitations of traditional manufacturing processes.
This digital leap both enhances operational efficiency and significantly improves product quality and worker safety, All the while setting a new standard in manufacturing excellence.
How Scout Systems Facilitates Digital Transformation
Scout Systems stands as a beacon for manufacturers aiming to navigate the complex journey of digital transformation. Our approach is unique and grounded in a deep understanding of manufacturing challenges and opportunities.
First and foremost, Scout Systems recognizes that each manufacturing entity has distinct needs and targets. We begin every project by gaining a profound comprehension of what you, as our client, need to achieve. This isn't about deploying generic software solutions; it's about crafting a path that aligns with your specific goals and challenges.
Our method is collaborative and supportive. Unlike other systems that may overwhelm you with complexity and jargon, Scout Systems ensures that the transition to digital is smooth and understandable. We invest time in educating and integrating your workforce into the digital transformation journey. This not only minimizes resistance but also fosters a culture of innovation and continuous improvement within your team.
Furthermore, Scout Systems prioritizes operational improvements and waste reduction from day one. Our digital solutions are designed to identify and eliminate inefficiencies, translating into immediate productivity gains and cost savings. This is not just about technology; it’s about transforming your operational ethos.
By providing clear, user-friendly digital work instructions, we enable rapid onboarding and cross-training of employees. This flexibility ensures your workforce can adapt quickly to changes, maintaining high levels of efficiency and productivity.
Scout Systems is more than a vendor; we are a strategic partner committed to your success. We guide, support, and empower your journey towards a digital future, ensuring that you are not just surviving but thriving in the competitive manufacturing landscape.
Key Benefits of Implementing Manufacturing KPIs
Implementing manufacturing KPIs through digital solutions provides numerous benefits, enhancing operational efficiency, productivity, and overall performance. Here are the key advantages:
- Real-time Monitoring and Control: Digital solutions enable real-time tracking of manufacturing processes. This immediate feedback allows for swift adjustments, reducing downtime and enhancing productivity.
- Data-driven Decision-making: With KPIs digitally tracked, decisions are based on accurate, timely data rather than assumptions or outdated information. This leads to more strategic, effective decision-making processes.
- Increased Efficiency and Productivity: By monitoring KPIs such as cycle time, throughput, and quality rates, manufacturers can identify bottlenecks and inefficiencies. Digital tools help streamline operations, leading to improved productivity and reduced costs.
- Quality Improvement: Digital manufacturing KPI tracking enables quick identification and rectification of quality issues. Continuous monitoring ensures products meet quality standards, reducing waste and rework.
- Enhanced Customer Satisfaction: Meeting delivery deadlines and maintaining product quality leads to higher customer satisfaction. Real-time KPI tracking allows for better project management and customer service.
- Predictive Maintenance and Downtime Reduction: Digital solutions can predict equipment failures before they occur, scheduling maintenance more effectively and avoiding unplanned downtime.
- Better Resource Allocation: By understanding which areas are underperforming through KPI analysis, companies can allocate resources more effectively, ensuring that efforts are directed where they are most needed.
- Improved Safety and Compliance: Safety metrics can be continuously monitored, ensuring workplace safety and compliance with regulations, leading to a safer work environment.
- Transparency and Accountability: Digital KPI tracking provides transparency, allowing team members at all levels to understand their performance and how it aligns with organizational goals, fostering a culture of accountability and continuous improvement.
Scalability and Flexibility: Digital solutions adapt to changing business needs, allowing for scalability. As the company grows or changes, so too can the KPIs and metrics tracked, ensuring they always align with current business objectives.
How to Select Manufacturing KPIs for Driving Operational Excellence
Approaches to selecting impactful Key Performance Indicators (KPIs) and balancing between value-add and non-value-add activities are essential steps toward driving operational excellence in manufacturing.
The selection of impactful KPIs must be aligned with the overall goals and strategy of the manufacturing operation. Identifying KPIs that directly correlate with the core objectives of the business ensures that the metrics monitored are meaningful and contribute to overall success.
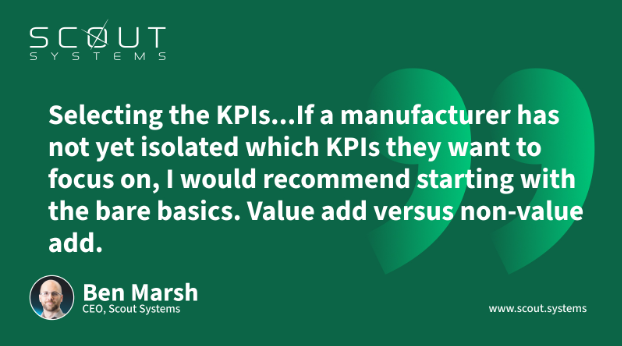
In the realm of manufacturing, distinguishing between value-added and non-value-added activities becomes a critical factor in operational efficiency. Value-add activities are those that directly contribute to the final product or service, enhancing customer value.
Non-value-added activities, on the other hand, do not add value to the end product and should be minimized or eliminated. Balancing these activities requires a keen understanding of the production process and an ability to identify areas of waste and inefficiency.
Implementing KPIs effectively involves continuous monitoring and evaluation. It is not enough to simply set targets; manufacturers must establish a system for regular review and adjustment of KPIs based on performance data and changing business objectives. This dynamic approach ensures that KPIs remain relevant and focused on driving improvement.
Moreover, fostering a culture of continuous improvement and employee engagement in the manufacturing process encourages ownership and accountability at all levels of the organization. When employees understand how their actions impact key metrics, they are more likely to focus on value-added activities. This focus will support the company’s goals for operational excellence.
Addressing Common Challenges with Digital Manufacturing KPIs
In the dynamic world of digital manufacturing, Key Performance Indicators (KPIs) are essential for tracking progress, production efficiency, and driving strategic decisions. However, organizations often encounter challenges in implementing and leveraging these metrics effectively. Here’s how to address common issues:
- Data Overload: The digital landscape produces vast amounts of data, leading to confusion and analysis paralysis. To counter this, prioritize KPIs that directly impact your strategic goals. Use data aggregation tools and dashboards to filter out noise and focus on actionable insights.
- Lack of Real-time Data: Delayed data can lead to missed opportunities and reactive rather than proactive decision-making. Implement real-time monitoring systems and IoT devices to provide instant data access, enabling timely actions and adjustments.
- Inconsistent Metrics Across Departments: Discrepancies in KPI definitions and calculations can lead to misalignments and inefficiencies. Standardize KPI definitions across all departments and ensure clear communication and training on how each metric is measured and used.
- Poor Data Quality: Inaccurate or incomplete data can skew results and lead to wrong decisions. Establish rigorous data validation and cleaning processes. Regularly review and maintain data sources to ensure reliability and accuracy.
Resistance to Change: Employees may be skeptical or resistant to new KPIs and technologies. Address this by involving team members in the KPI development process, providing adequate training, and demonstrating the tangible benefits of these metrics on their work and overall company success.
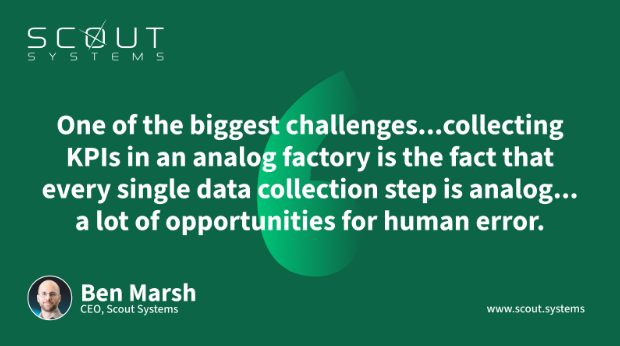
By tackling these challenges head-on, companies can harness the full potential of digital manufacturing KPIs, driving improvement, innovation, and production processes.
Overcoming Data Overload and Integration Challenges
Let’s explore the hurdles of data overload and integration challenges even more deeply. How can Scout Systems help you navigate this new landscape effectively?
First, tackle data overload with focus. Instead of drowning in numbers, identify your main goals. What drives your factory's growth? Once clear, use this as a beacon to sift through data, seeking out what genuinely advances your objectives. This precision cuts through the clutter, aligning data analysis with your strategic targets.
Integration presents another layer of complexity. Merging different tools and systems can feel like a maze. Scout Systems simplifies this process. Start by mapping out your integration journey. Which data needs transferring? What insights are you aiming to gain? Address these questions methodically, moving data piece by piece to avoid overwhelm.
Moreover, engage with your workforce during these changes. Clear communication transforms resistance into cooperation. Educate your team not just on the 'how' but the 'why' behind digital transitions. This understanding fosters a collaborative environment, easing the adoption of new practices.
By approaching these challenges with a targeted, methodical, and inclusive strategy, Scout Systems not only enhances your manufacturing efficiency but also paves the way for a smoother digital transformation. Embrace the shift with clarity and collaboration, and watch your production hurdles become milestones.
Embracing Change: Overcoming Resistance in Digital Transformations
Digital transformations often encounter resistance, a natural human response to change rooted in uncertainty and fear of the unknown. Understanding this resistance is the first step towards addressing it. It's essential to communicate the benefits clearly and ensure transparency throughout the transformation process.
Leaders play a pivotal role in navigating this change. By fostering a culture of continuous learning and adaptability, they can mitigate fears and build an environment that embraces innovation. It's not just about introducing new tools or processes; it's about shifting mindsets and encouraging a culture of experimentation and learning.
Challenges of Change in Manufacturing
Moreover, involving employees in the transformation process can significantly reduce resistance. When individuals feel they have a stake in the outcome, they are more likely to embrace change. This involvement can take many forms, from soliciting feedback to offering training that equips employees with the necessary skills for the new digital landscape.
Lastly, acknowledging the challenges and addressing them head-on can pave the way for a smoother transition. It's about creating a support system that helps employees navigate the uncertainties of change. By doing so, businesses can turn resistance into readiness, ensuring that their digital transformation journey is not just about surviving but thriving in the new digital era.
Empowering the Workforce: Education and Training in the Digital Age
In the rapidly evolving landscape of the digital age, the empowerment of the workforce through education and training stands as a pivotal cornerstone. As technology continues to reshape industries, the demand for a skilled workforce adept in digital literacy and equipped with cutting-edge knowledge has never been higher.
Empowering the workforce in this digital era goes beyond traditional training; it encompasses a holistic approach that merges technical skills with soft skills development. It's about creating a learning culture within organizations. Continuous improvement and innovation are not just encouraged but embedded into the very fabric of the workplace.
Education and training programs in the digital age must be dynamic, flexible, and tailored to meet the diverse needs of employees. They should provide a blend of online learning platforms, hands-on workshops, and real-world application opportunities. This multi-faceted approach facilitates not just the implementation of digital competencies but also improves critical thinking, problem-solving, and collaborative skills.
Moreover, empowering the workforce is about inclusivity and accessibility. It involves designing programs that cater to different learning styles and levels of expertise. It ensures that all employees, regardless of their background or position, have the opportunity to grow and excel.
As we move forward, the role of leadership in fostering an environment of learning and development cannot be overstated. Leaders must champion the cause of education and training, providing the necessary resources, support, and encouragement for their teams to thrive in the digital age.
Ultimately, empowering the workforce through education and training is a strategic investment in the future. It enhances individual careers and drives organizational success, innovation, and competitiveness in an increasingly digital world.
Future-Proofing Your Manufacturing Operations
Future-proofing your manufacturing operations is more than a mere buzzword; it's an essential strategy in today's rapidly evolving industrial landscape. As technological advancements and market dynamics shift at an unprecedented pace, manufacturers must adopt a proactive approach to stay ahead. This involves integrating smart technologies and sustainable practices to ensure resilience and competitiveness.
One critical aspect of future-proofing is embracing digital transformation. By leveraging data analytics and IoT (Internet of Things), manufacturers can gain real-time insights into their operations. This enables predictive maintenance and optimized production processes.
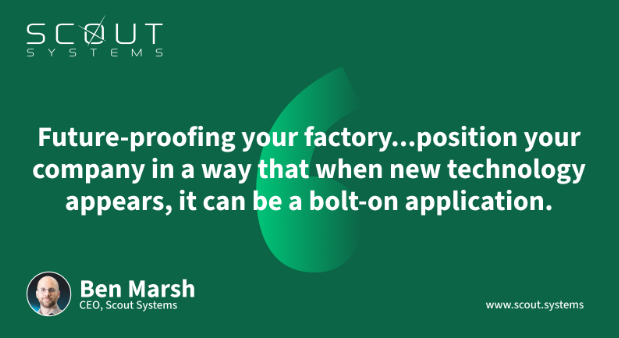
Sustainability is another pillar of future-proofing manufacturing operations. As environmental regulations tighten and consumer preferences shift towards eco-friendly products, manufacturers must adopt green technologies and circular economy principles. This not only mitigates environmental impact but also aligns with the growing demand for sustainable manufacturing practices.
Finally, collaboration with stakeholders, from suppliers to customers, is essential. Building strong relationships and open communication channels enables manufacturers to respond swiftly to market changes and customer demands. By fostering a culture of innovation and continuous improvement, manufacturers can not only survive but thrive in the future industrial landscape.
Stay Ahead of the Curve with Manufacturing KPIs
In conclusion, leveraging Manufacturing KPIs is not just a trend but a strategic imperative for businesses aiming to stay competitive in the fast-paced manufacturing sector.
As outlined, effective use of KPIs enables companies to:
- Streamline operations
- Boost efficiency
- Enhance product quality
By focusing on critical metrics such as operational efficiency, quality rates, and customer satisfaction, manufacturers can pinpoint areas needing improvement, optimize processes, and ultimately drive profitability.
Furthermore, integrating advanced technologies and embracing continuous improvement cultures amplifies the benefits of KPIs. It allows for real-time data analysis and informed decision-making. Companies that adopt these measures can anticipate market changes more accurately, respond to customer needs swiftly, and maintain a competitive edge.
In essence, Manufacturing KPIs are not just indicators but catalysts for growth and innovation. By committing to a data-driven approach, manufacturers can ensure sustainability, adaptability, and success in an ever-evolving industry landscape. And Scout Systems is here to help you with that. Contact us to learn more.
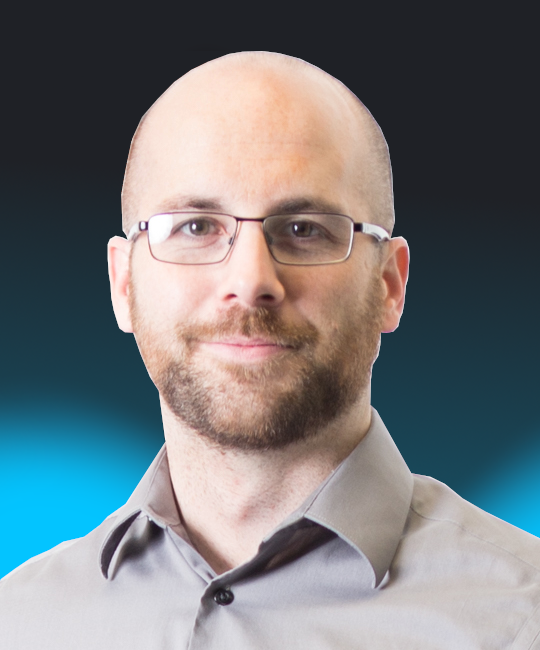
Ben Marsh
I've spent my career in Manufacturing, and can't stop trying to make things more efficient. At home, I am a master Lego builder with my son.