Key Performance Indicators (KPIs) are measurable values that demonstrate how effectively an manufacturing organization is achieving its key business objectives. Manufacturing operations use these metrics at multiple levels to evaluate their success at reaching targets. In this post I want to cover some manufacturing KPIs that I have found to be exceptionally useful for manufacturing facilities to implement to boost efficiency and quality.
4 Manufacturing KPIs you must track today
As with all metrics, those used to measure and track a manufacturing facility can vary in complexity. However, these are the essential manufacturing KPIs that I recommend for all production facilities focused on process improvement:
- Cycle Time - In manufacturing, Cycle Time is defined as the total time it takes to produce a product from the beginning of the production process to its completion. This metric encompasses the entire production cycle, including the time spent on each step or process involved in manufacturing the product.
To measure Cycle Time, you can use one of the following two methods:
- Individual Unit Method
- Formula: Cycle Time = Unit Complete Time - Unit Start Time
- Benefit: This method allows you to calculate the standard deviation, providing greater confidence in the quality and consistency of your data.
- Order-Based Method
- Formula: Cycle Time = (Order Complete Time - Order Start Time) / Total Units in Order
- First Pass Yield (FPY) - This represents the percentage of products that are manufactured correctly and meet quality standards for the first time through the production process, without requiring any rework or repairs.
Formula: First Pass Yield (FPY) = (Number of Good Units Produced / Total Number of Units Entering the Process) x 100
A high First Pass Yield (FPY) indicates that the manufacturing process is producing high-quality products consistently.
- Production Gaps - This metric refers to the lost labor time that occurs between the completion of one production order and the start of the next. This downtime is a critical metric, as it directly impacts overall production efficiency. Addressing production gaps is often one of the simplest improvements to make, primarily through the optimization of communication and coordination within the production process.
Formula: Production Gap = Start Time of Second Order - End Time of First Order
- Takt Time - One of the key metrics of Lean Manufacturing, defining the rate at which a finished product needs to be completed in order to meet customer demand. It is used to synchronize production processes and ensure that the manufacturing pace aligns with the customer needs.
Formula: Takt Time = Available Production Time / Customer Demand
By combining Takt Time with Cycle Time and First Pass Yield (FPY), manufacturers can conduct a comprehensive performance analysis. This comparison helps them evaluate the alignment between the required production rate and the actual production rate, providing insights into efficiency and quality.
Manufacturing KPIs for Operation Excellence
Achieving operational excellence often necessitates technological assistance to accurately and consistently record metrics. Many manufacturers leverage SOP software with integrated machine monitoring to streamline the data collection process. As we review these next manufacturing KPIs, it's important to recognize that achieving these metrics can be labor-intensive in a traditional, analog factory setting.
- Overall Equipment Effectiveness (OEE) - A comprehensive manufacturing KPI used to evaluate the efficiency and productivity of equipment/cells. It provides insight into how effective a manufacturing operation is by measuring three primary factors:
- Availability: Measures the percentage of scheduled time that the equipment/cell is available for production. It accounts for downtime due to failures, setup, and adjustments.
Availability = (Operating Time / Planned Production Time) x 100
- Performance: Measures the speed at which the equipment/cell operates compared to its designed speed. It accounts for slow cycles and small stops.
Performance = ((Ideal Cycle Time x Total Units) / Operating Time) x 100
- Quality: Measures the percentage of good units produced out of the total units started, accounting for defects and rework (same as First Pass Yield)
Quality = (Good Pieces / Total Pieces) x 100
With those three benchmarks we can now calculate the Overall Equipment Effectiveness (OEE).
Formula: OEE = Availability x Performance x Quality
- Waste and Root Cause - Referring to any activity or process that does not add value to the product or service from the customer's perspective. Identifying and eliminating waste is crucial for improving efficiency, reducing costs, and increasing overall productivity. Root Cause analysis involves identifying the underlying reasons for the presence of waste or any other inefficiencies within the manufacturing process.
Regularly reviewing your average amount of Waste should serve as a critical benchmark for your manufacturing processes. Using Root Cause analysis as a tool to identify and address the underlying reasons for waste will help in systematically reducing total waste and enhancing overall efficiency.
Returning to the importance of utilizing SOP software with built-in data collection, such a system significantly simplifies and enhances the accuracy of information gathering. While measuring obvious waste is straightforward, a digital platform helps uncover hidden waste embedded in work processes, making it easier to identify and address inefficiencies.
- Manufacturing Cycle Efficiency - A key performance indicator that measures the efficiency of the production process by comparing the value-added time to the total production time. It provides insights into how much of the total production time is actually spent on activities that add value to the product, as opposed to the time spent on non-value-added activities such as waiting, transporting, and inspecting.
Formula: Manufacturing Cycle Efficiency = (Value-Added Time / Total Production Time) x 100
As mentioned earlier, SOP software enables Manufacturing Engineers to better visualize production data, allowing them to accurately identify and understand which elements of the process constitute value-added time.
Manufacturing KPIs for Production Management
When immediate reactionary decisions are required, having the right manufacturing KPIs readily available ensures that management can make informed decisions swiftly and accurately. Capturing these metrics is not only recommended but essential for effective decision-making. Implementing these KPIs into real-time dashboards can significantly enhance processing speed and responsiveness, allowing management to address issues promptly and maintain optimal production efficiency.
- Work-in-Progress (WIP) Value - The items in the production process that are not yet completed. These items have moved beyond the initial stages of production but are not yet finished products. WIP is a critical component of inventory management and production planning, as it represents the intermediate stage of manufacturing. Leveraging APIs and interconnecting your shop floor management system with your ERP can allow you to calculate the WIP values in real-time.
Formula: WIP Value = Consumed Material Costs + Completed Labor Costs + Allocated Overhead
Comparing the current WIP valuation to the expected production cost of goods provides a percentage that indicates how close a product is to completion. This metric can significantly enhance the efficiency of production schedulers and help avoid the risk of damaging expensive WIP. By monitoring this percentage, managers can make more informed decisions about resource allocation, production timelines, and potential bottlenecks, ultimately optimizing the entire production process.
- Throughput - A measurement of production efficiency, referring to the rate at which a system produces finished goods over a specific period of time. Essentially, it represents the number of units produced per unit of time.
Formula: Throughput = Total Units Produced / Total Production Time
This benchmark is best when paired with the next manufacturing KPI.
- Rolling Throughput Yield - Used in manufacturing and process improvement to measure the cumulative quality and efficiency of a series of processes or production steps. It reflects the likelihood that a product will pass through the entire production process without defects, considering each stage's yield. RTY is particularly useful in identifying the impact of multiple stages on the overall production yield and quality.
Calculating the Rolling Throughput Yield involves 2 different formulas: 3. Formula for Yield = Number of Good Units Produced / Total Number of Units Processed
- Formula for RTY = (Yield of Step 1) x (Yield of Step 2) x … x (Yield of Step n)
When combined with Throughput, management can confidently estimate both the current rate at which good parts are exiting the manufacturing process and the expected rate at which they should exit. This comprehensive view enables better decision-making, improved production planning, and enhanced ability to meet customer demand efficiently.
- Manufacturing Cycle Efficiency (MCE) - Measures the proportion of time spent on value-added activities relative to the total production cycle time. It provides insight into how efficiently the production process is operating by highlighting the percentage of time that directly contributes to the creation of the product. This calculation works best when digital work instructions (or alternative data collection systems) is being used to measure waste in real-time to allow you to extract the value-add.
Formula: MCE = (Value-Added Time / Total Production Time) x 100
Manufacturing KPIs to Prepare for the Future
In the rapidly evolving landscape of manufacturing, staying ahead of technological advancements is crucial for maintaining competitiveness and achieving long-term success. The following metrics are essential for measuring how prepared your manufacturing operation is to adapt to new technological advancements and thrive in the future.
Digital Transformation Index (DTI)
The Digital Transformation Index (DTI) measures the progress of an organization's digital transformation journey. It assesses the integration of digital technologies into various aspects of the business, from operations to customer engagement. A high DTI score indicates a robust digital strategy and a readiness to leverage digital tools for improved efficiency and innovation.
- Components of DTI: This includes digital infrastructure, digital strategy and leadership, operational efficiency, customer experience, innovation and agility, and workforce and culture.
- Benefits: A higher DTI score can lead to enhance productivity, reduced costs, and better ability to respond to market changes.
Supply Chain Efficiency (SCE)
The Supply Chain Efficiency (SCE) measures how effectively your supply chain operates, from sourcing raw materials to delivering finished products to customers. It involves optimizing logistics, reducing lead times, and ensuring a seamless flow of goods and information.
- Components of SCE: Inventory turnover, order fulfillment time, and supplier reliability.
- Impact: Efficient supply chains reduce costs, minimize waste, and ensure timely delivery, contributing to overall operational excellence.
AI/Automation Adoption Rate
The AI/Automation Adoption Rate tracks the extent to which advanced technologies have been implemented in your manufacturing process. This metric indicates your organization's readiness to harness the benefits of cutting-edge technologies.
- Components of Adoption: This includes robotics for assembly lines, AI-driven quality control, predictive maintenance, and automated data analysis.
- Advantages: Increased adoption of AI and automation can lead to higher productivity, reduced error rates, enhanced scalability, and significant cost savings.
How To Score Each of these Metrics
Since each factory has unique needs and opportunities, the metrics listed above must be custom scored to accurately reflect individual circumstances. Despite the need for customization, the approach to scoring remains consistent across all metrics, following these steps:
Identify specific metrics for each component and assign a weight to each based on its importance to your organization. Additionally, set a priority percentage for each main category to reflect its overall significance. The total priority across all categories should equal 100%.
Example using Digital Transformation Index (DTI) with Category Priority Weight of 50%
Assumptions: DTI can be broken into Digital Infrastructure and Digital Strategy categories.
List and weight the sub-components of the two categories:
Digital Infrastructure: Cloud Adoption (4), SOP Software (3), IoT Integration (2), Cyber Security (4) Weighted Score: (4 + 3 + 2 + 4) / 4 * (Priority 50%) = 1.625
Digital Strategy: Digital Strategy (4), Leadership commitment (5), Governance framework (4) Weighted Score: (4 + 5 + 4) / 3 * (Priority 50%) = 2.166
Aggregate Score: 1.625 + 2.166 = 3.791 (out of a possible 5.00)
A higher aggregate score indicates a high level of integration, suggesting that the organization is well-prepared for future technological advancements. Areas with lower scores might need more focus to improve overall digital maturity.
By regularly measuring and analyzing these scores, organizations can track their transformation progress, identify areas for improvement, and make informed strategic decisions to enhance their capabilities.
Getting Started with a Strategic Partner
Utilizing manufacturing KPIs is a powerful strategy to enhance the efficiency and quality of your operations. When resources are limited, crafting a roadmap becomes essential to establish a strong foundation for your transformation. If you want to move quickly, at Scout Systems, we provide a money-back guaranteed digital transformation through our Accelerator Program. Our team collaborates closely with yours to align key objectives and offers comprehensive support through planning, configuration, training, installation, and data analytics. Your factory will see immense transformation in just 90 days.
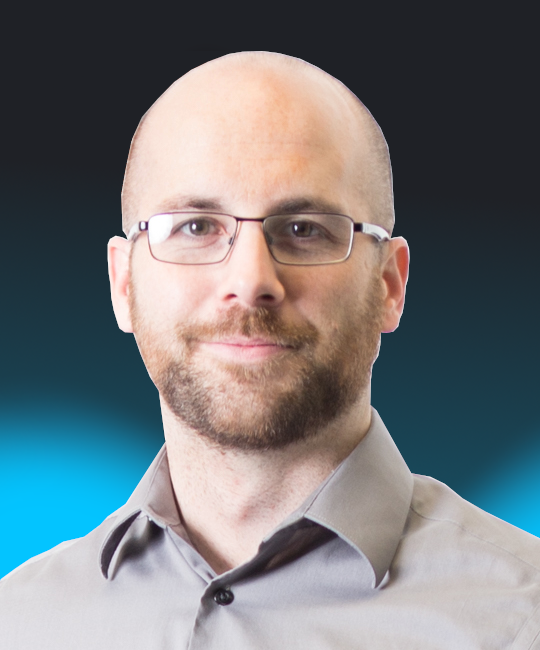
Ben Marsh
I've spent my career in Manufacturing, and can't stop trying to make things more efficient. At home, I am a master Lego builder with my son.