Delivering enhanced flexibility to customers brings forth a unique array of challenges. With the rise in customer demand for a wider range of products, low volume, high mix production environments are becoming increasingly prevalent. Amidst the mounting challenges faced by manufacturers, there's a growing expectation for consistent, if not improved, quality and efficiency standards.
By integrating Scout Systems' Work Instruction Software, particularly leveraging its Variant feature, manufacturers can effectively navigate this complexity. This strategic utilization not only streamlines operational chaos but also lightens the burden on manufacturers, facilitating smoother production processes.
Understanding Low Volume High Mix Production
Low volume high mix production is characterized by the manufacture of a wide variety of products in relatively small quantities, demanding precision and versatility from manufacturers. This model necessitates a flexible production approach to accommodate the frequent changes in product specifications and orders that are commonplace in industries such as aerospace, medical devices, and custom manufacturing.
The inherent complexity of this production type lies in managing the diversity of product configurations while maintaining efficiency. The key challenge is striking a balance between customization and standardization in the production process to ensure optimal resource utilization and customer satisfaction.
Defining the Production Model
Low volume high mix production involves crafting diverse products in modest quantities, demanding adjustable processes and sophisticated management methods to maintain efficiency and meet bespoke client requirements.
This manufacturing strategy seeks a delicate equilibrium between flexibility and standardized workflows, vital for success in sectors with frequent shifts in product demand, such as aerospace and medical equipment.
Every product variation brings a unique set of challenges and opportunities for innovation and customization.
Firms leveraging Scout Systems' Work Instruction Software with the Variant feature can significantly reduce complexity. By consolidating product families into single instructions and integrating APIs, operators receive precise, pre-selected work guidance, trimming documentation and elevating productivity.
Challenges in Diverse Manufacturing
Manufacturers embarking on low volume high mix production face a conundrum of rapid adaptation. They must adjust processes for varied, custom orders while maintaining high quality and cost control.
The shift between products necessitates recalibrations, threatening lean operation principles essential for optimal performance.
As product variables increase, the risk of operational inefficiency escalates. Complexity multiplies with each additional product requirement, straining traditional documentation and training approaches.
Consequently, the integration of customizable, precise work instructions becomes paramount. Scout Systems' Variant feature in Work Instruction Software attains this, enhancing operator performance by tailoring instructions to the specific product iteration at hand. This convergence of adaptability and standardization is a cornerstone for thriving in high variability markets where documentation overload and misinterpretation can sabotage throughput and quality.
Streamlining with Scout Systems' Variant Feature
Scout Systems' Variant feature departs from the conventional structure of work instructions by enabling users to create instructions for individual tasks rather than for the final product. Similar to universal tooling or common parts, these tasks can then be integrated into product instructions, reducing repetitive work for staff overseeing documentation control.
In low volume, high mix operations, Variant instructions can be further enhanced to accommodate specific steps in the process with multiple options. For instance, in an assembly where a choice between a 12-volt motor or a 24-volt motor is present, the same instruction can be utilized, but it can dynamically select the correct motor to align with the sales order.
To enhance this capability further, an entire work instruction could be crafted as a comprehensive set of Variants. This enables a single work instruction to manage an entire matrix of product selectors, providing a seamless and efficient solution for handling diverse product configurations.
Create Task Work Instructions
To get started, HQ Designers should create a work instruction dedicated solely to a task unique to each production option. For example, if there are three potential wiring harness configurations, each should have its own separate work instruction.
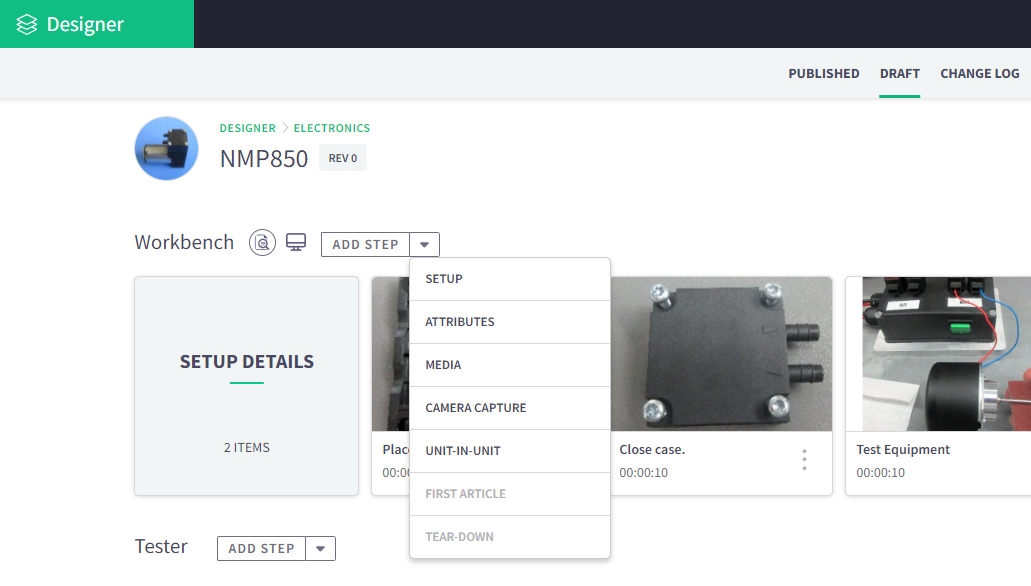
These tasks can then be designated to be hidden from Compass via Attributes, preventing Operators from inadvertently accessing partial work instructions. They are only made accessible when embedded into a completed product.
Embedding Unit-In-Units
After implementing task-based work instructions, users can proceed to create the final production work instruction. As required, the task-based instructions can be imported and seamlessly integrated into the instruction set using the Unit-in-Unit feature. This process inserts a Read-Only version of the instruction into the new one, ensuring smooth incorporation of essential task details.
It's important to note that if changes are required in the task-based work instructions, they must be made directly in the original file. Any modifications made to the original file will be globally updated across all instructions that have the file embedded within them.
Creating Variation
Expanding a manufacturing work instruction to include Variants is remarkably straightforward. After embedding a Unit-in-Unit, users can effortlessly add Variants by selecting the three-dot menu and clicking on "Add Variant." This allows users to incorporate as many Variants as necessary with ease.
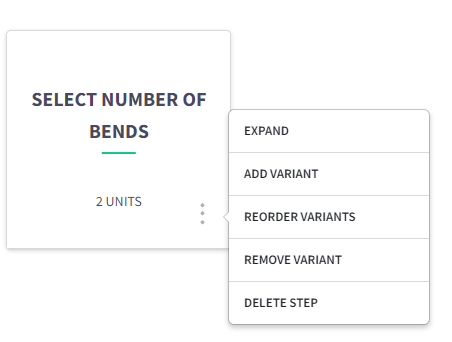
Integrating Variant with Production Automation
After publishing a work instruction with embedded variants, Operators can access and load the file from their Compass work station. Upon reaching the Variant step, Operators will be presented with their options and prompted to select the Variant necessary to complete their process. However, this manual step may introduce human error. To mitigate this risk, it is recommended to implement API integration and leverage Variant Selection to automatically select the required steps in alignment with the order in the ERP system. When implemented correctly, Operators can effortlessly receive work instructions tailored to guide them through a custom order without any additional effort.
The Impact of Documentation Reduction
By drastically reducing the volume of documentation required, the cognitive load on operators is significantly lessened. A leaner document repository aids in faster information retrieval, streamlining the onboarding of new staff and reducing the occurrence of errors due to document mismanagement or outdated versions. This consolidation of information into a single, accessible resource is instrumental in boosting productivity and maintaining a high standard of quality.
The advantage of Variant's integrative document reduction is epitomized through the reduction of training time and material waste. A "one instruction fits all" solution adapts seamlessly to the frequent shifts intrinsic in low volume high mix manufacturing. Consequently, the precision and consistency of product assembly are enhanced, as operators are presented with meticulously tailored instructions that require minimal time to interpret and implement, resulting in an efficient production cycle that far exceeds conventional methods.
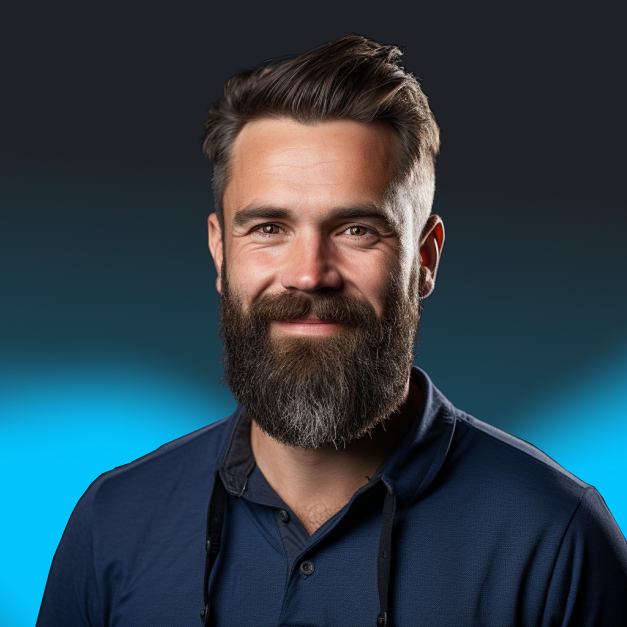
Richard Mason
By day I help people solve problems, by night I'm enjoying IPAs! For fun I work in my garage building gadgets that cost way more than they are worth.