Once, a clockmaker adjusted his gears and springs, ensuring each tick matched the tock precisely.
This meticulous calibration mirrors the essence of Lean Manufacturing, fine-tuning production to customers' rhythms.
In harnessing Lean principles, assemblers and fabricators sculpt workflows that whisper of efficiency, where excess falls away, and value emerges uncluttered.
Key Principles of Lean Manufacturing
In the pursuit of excellence within Lean Manufacturing, five key principles pave the road to optimized production. These quintessential tenets aim to streamline processes, eliminating waste and amplifying value. Every gear in the assembly line is examined for its contribution to flow, and adjustments are meticulously made to ensure that each action taken contributes positively to the end result. This relentless focus on continuous improvement, known as Kaizen, demands a culture that incessantly seeks to refine and enhance every aspect of operations.
Underpinning these key principles is a thorough understanding of value from the customer's perspective, often referred to as the Value Stream. It is through this lens that one can dissect and scrutinize every process, separating necessary functions from superfluous activities. In essence, Lean Manufacturing is not a mere collection of tools but a philosophical approach that insists on a relentless quest for perfection. It is a methodical march towards the elimination of all forms of waste, synchronizing every stroke of work with the cadence of customer demand, and in doing so, sculpting a masterpiece of operational excellence.
Value from a Customer Perspective
In Lean Manufacturing, the term "value" is inherently defined by the customer's needs and preferences, which dictate production design and processes. Value constitutes the attributes for which a customer is willing to pay.
It is critical for assemblers and fabricators to internalize the buyer’s valuation as a compass for operational activities. Anything not contributing to this perceived value is deemed as "waste" and slated for elimination in the quest for process purity.
Lean efforts synchronize product features with customer desires to eliminate wasteful practices.
Thus, understanding customer value is not static; it demands constant vigilance and adaptation. As preferences shift and markets evolve, maintaining alignment with customer value becomes an enduring task. Scrutinize your production through this lens to ensure operative alignment with customer expectations and demands.
The Five Steps of Value Stream Mapping
Value Stream Mapping (VSM) is an integral tool for visualizing and optimizing processes from start to finish.
- Identify the product family: Group similar products that can undergo the same processes.
- Map the Current State: Document all the steps, delays, and information flows currently in use.
- Analyze the Current State: Identify waste and areas for improvement within the existing system.
- Design the Future State: Create a streamlined process that eliminates waste and maximizes value.
- Develop an Implementation Plan: Structure the approach for transitioning to the future state design.
By mapping the current state, inefficiencies are brought to light, prompting strategic discussions.
Appropriately addressing these inefficiencies, the Future State map turns into a blueprint for leaner operations.
Optimizing Workflow Efficiency
The quintessence of Lean Manufacturing pivots on relentlessly pursuing the enhancement of workflow efficiency, ensuring that each component, action, and procedure synergistically contributes to a fluid operational tempo. Through rigorous application of Just-In-Time principles, manufacturers can synchronize production schedules with demand, thus minimizing idle resources and reducing throughput times. By leveraging Poka-Yoke mechanisms, they can also mitigate errors, fostering a quality-centric atmosphere that bolsters both production consistency and customer trust. Moreover, an effective strategy often involves employing Kanban systems to visualize workflow and manage inventory with precision, ensuring that each workstation is primed for optimal performance without the encumbrance of excess material or information lag.
Just-In-Time (JIT) Production Explained
Just-In-Time represents an operational tour de force.
Within the pantheon of lean methodologies, Just-In-Time stands as a paragon of operational efficiency. Its underlying philosophy revolves around producing goods precisely when they are needed and not before, thereby minimizing inventory costs and fostering streamlined manufacturing processes. Consequently, JIT is the epitome of efficiency, eliminating wastefulness associated with overproduction, excess inventory, and the associated carrying costs.
Inventory, only when required, underpins JIT.
Proper implementation of JIT necessitates a paradigm shift - away from traditional batch-and-queue production methods toward a flow that aligns more intimately with customer demand. This requires robust coordination with suppliers and a keen understanding of the production process to ensure timely delivery of parts just as they are needed – avoiding both wastage and downtime.
Lean principles writ large within JIT dynamics.
The efficacy of JIT is anchored in its demand-driven approach, which harmonizes production with actual consumption patterns, thus dodifying the perils of forecasting errors and overstock. By embracing a JIT strategy, fabricators and assemblers can enhance their responsiveness to market shifts and customer needs, resulting in a competitive edge in the rapidly evolving manufacturing landscape.
JIT shores up strategic responsiveness and resource allocation.
JIT's tenets are critically aligned with the imperatives of modern manufacturing practices, reflecting a trajectory towards greater agility and waste minimization. As we progress beyond 2023, this manufacturing ethos continues to influence a broad swathe of industry sectors, underpinning the transformative shift towards more sustainable production paradigms and heightening the emphasis on precision-timed supply chains.
The Impact of Pull Systems
Pull systems revolutionize inventory management by aligning production with actual demand rather than forecasts.
- Just-In-Time Production: Ensuring products are created as needed, reducing inventory costs.
- Waste Reduction: Minimizing overproduction and subsequent waste, adhering to lean principles.
- Enhanced Flexibility: Allowing rapid adaptation to changing customer demands and market conditions.
- Customer-Centric: Focusing on customer needs, improving satisfaction and loyalty.
- Resource Optimization: Streamlining the use of materials and resources, promoting efficient operations.
Pull systems epitomize operational efficiency and customer responsiveness.
Embracing pull systems can markedly elevate a manufacturer's competitive stance in a volatile market.
Eliminating Waste with Kaizen
Kaizen, a cornerstone of lean manufacturing, represents continuous improvement in pursuit of ultimate efficiency. It focuses on streamlining processes to eliminate waste or "muda," thereupon boosting an organization's performance and competitiveness.
In practical terms, Kaizen fosters a culture where all employees are actively engaged in suggesting and implementing improvements. This collective effort helps identify and eradicate non-value-adding activities, thereby accelerating the journey toward operational excellence.
The essence of Kaizen lies in its incremental, yet relentless, approach to waste elimination. This iterative process perpetuates a cycle of refinement and enhancement, driving the transformation toward leaner, more agile manufacturing.
The Seven Wastes in Lean
Transport reflects unnecessary movement of materials.
In Lean, the concept of Inventory encompasses more than stocked goods. It refers to any supply in excess, which ties up capital, incurs storage costs, and may lead to deterioration or obsolescence. Likewise, Motion waste emerges when workers make unnecessary movements, which can lead to inefficiency and increase the risk of injury. Reducing such wasteful motion is key to a more streamlined operation.
Waiting embodies idle time where resources are not active.
Unnecessary Processing is often due to poor tool or product design and leads to wasted time and resources. Overproduction, manufacturing items before they're needed, inherently creates additional waste - it requires excess storage, increases handling, and compounds the risks associated with inventory waste. Finally, Defects entail the time and materials spent on products that fail to meet quality standards.
In our pursuit of efficiency, it's imperative to address these forms of waste through Lean methodologies that streamline operations, driving the transformation toward an optimized manufacturing landscape. Recognizing and eliminating these wastes can play a pivotal role in a company's journey to operational excellence, especially in the lean-focused climate of 2023. Indeed, excising these inefficiencies can be a defining factor for success in a competitive manufacturing sector, highlighting the importance of integrating these principles into the fabric of production strategies.
Continuous Improvement with Kaizen
Kaizen, a cornerstone of lean methodology, champions the pursuit of continuous, incremental improvement.
- Emphasizing employee involvement at all levels
- Fostering a culture that encourages regular, small changes
- Improving productivity and efficiency through systematic, sustained efforts
- Reducing waste and enhancing quality consistently
This philosophy underpins a relentless drive toward perfection in manufacturing processes.
By making Kaizen an integral practice, assemblers and fabricators can achieve remarkable advancements in operational performance.
Achieving Flow and Quality
In lean manufacturing, flow signifies the seamless progression of materials and products through the production process without interruptions, delays, or bottlenecks. This uninterrupted cadence of operations is vital for maintaining a rhythm that aligns with customer demand, thereby optimizing throughput and minimizing waste.
Attaining consistent quality, on the other hand, necessitates rigorous adherence to standardized work procedures and a commitment to excellence across the board. It involves a comprehensive understanding of customer requirements, and the implementation of quality controls that identify defects at the source, preventing them from flowing downstream. This convergence ensures that efficiency does not come at the expense of product integrity.
Together, the concepts of "flow" and "right-first-time" are intertwined, representing a harmonious balance wherein efficiency and quality coexist without compromise, setting the foundation for a lean operation's enduring success.
The Role of Takt Time
In the realm of lean manufacturing, takt time represents the pulse of production, aligning manufacturing speed with customer demand. Precisely calibrating this metric is essential for synchronizing workflow and ensuring operational harmony.
Achieving a balanced work rate is contingent upon an accurate takt time calculation. It serves as a benchmark for production efficiency, guiding the pace at which workstations complete their tasks.
Integrating takt time into lean practices facilitates the adjustment of production rates to meet shifts in customer demand. This adaptable tempo allows for just-in-time delivery, minimizing the risk of overproduction or shortages that could disrupt the flow.
Consequently, takt time is instrumental when scaling up or dialing down production volumes in response to market fluctuations. By maintaining a consistent beat in the manufacturing process, organizations can ensure a smooth, lean operation that adheres to the principles of continuous flow and waste reduction. In essence, takt time is the "metronome" that orchestrates the timely execution of all production activities.
Jidoka: Automation with a Human Touch
Jidoka represents the concept of intelligent automation, blending mechanical efficiency with human oversight to ensure product integrity. This principle is foundational to lean manufacturing, providing a mechanism for quality assurance that is both proactive and responsive.
Driving this approach is the ability to halt production when an anomaly is detected, seamlessly integrating error detection with corrective action. By granting machines the autonomy to pause operations, immediate intervention is possible—tracing irregularities at their origin. This intersection of machine precision and human ingenuity is where Jidoka shines, empowering operators to address issues before they escalate into significant defects.
Moreover, Jidoka shifts the paradigm from a reactive to a proactive quality control stance. Instead of relying solely on end-of-line inspections, quality checks are interpolated throughout the production process. This preemptive strategy minimizes the risk of faulty products reaching downstream processes or, worse, the customer.
In essence, Jidoka facilitates a symbiotic relationship between automated systems and the human workforce. It reinvents how assembly and fabrication tasks are performed, ensuring that each step is under the vigilant scrutiny of both machine and operator. Incorporating Jidoka into production lines fosters a culture of continuous improvement, catalyzing efficiency gains while fortifying the commitment to deliver flawless products to the customer.
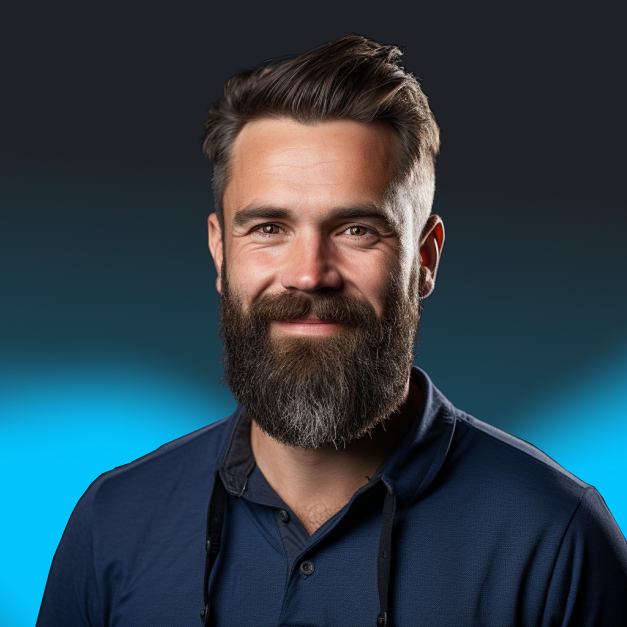
Richard Mason
By day I help people solve problems, by night I'm enjoying IPAs! For fun I work in my garage building gadgets that cost way more than they are worth.