In the face of mounting defects, manufacturers grapple with quality control, spiraling costs, and dissatisfied customers.
Six Sigma emerges as a beacon of efficiency, promising a systematic reduction in errors and operational excellence.
Adopting the Six Sigma DPMO metric offers a quantifiable approach to measuring defects, ensuring continuous improvement and customer satisfaction.
Fundamentals of Six Sigma
The inception of Six Sigma can be traced to a relentless pursuit of quality enhancements and process optimization. With its structured methodology and data-driven approach, Six Sigma aims to mitigate variances in manufacturing and business processes. This rigorously detailed framework focuses on reducing process variability which is pivotal in achieving the highest level of quality management.
Embracing Six Sigma principles involves a steadfast commitment to achieving near perfection. Utilizing advanced statistical tools, professionals aim to restrict defects to a mere 3.4 occurrences per million opportunities. This relentless striving for excellence underpins the remarkable efficiency gains and customer satisfaction advancements linked to Six Sigma adoption.
Essence of Six Sigma
Six Sigma is fundamentally about achieving precision and excellence within any given process.
At its core, Six Sigma enhances operational accuracy, vastly reducing the probability of defect occurrence.
By emphasizing a meticulous and data-centric methodology, Six Sigma facilitates the identification, analysis, and rectification of process defects, leading to improved quality outputs.
Through the rigorous application of Six Sigma principles, operations can attain unparalleled levels of defect minimization, fostering enhanced product integrity and boosting consumer confidence.
Key Principles and Methodologies
Six Sigma DPMO (Defects Per Million Opportunities) is grounded in methodologies that ensure quality and consistency.
- Define: Clearly articulate the problem, goals, and deliverables for any project or process improvement.
- Measure: Collect data and establish current performance baselines.
- Analyze: Examine the data to identify patterns, anomalies, and root causes of defects.
- Improve: Implement strategies for process enhancement and defect reduction.
- Control: Sustain the improved state with monitoring and ongoing management.
These steps comprise the DMAIC framework, integral to process optimization in Six Sigma.
Six Sigma also relies on rigorous training to develop subject matter experts known as Green Belts, Black Belts, and Master Black Belts.
Benefits for Organizations
Improved Quality Control: DPMO standards elevate an organization's product precision and quality. Streamlined Processes: Organizations optimizing with Six Sigma DPMO report dramatic efficiency gains across operations. Cost Reduction: Enhanced process efficiency leads to reduced waste, translating into significant cost savings for companies. Market Competitiveness: Adopting Six Sigma DPMO can result in superior products, propelling organizations ahead of competitors. Customer Satisfaction: A direct correlation exists between Six Sigma implementation and heightened customer contentment levels.
Decoding DPMO
DPMO, or Defects Per Million Opportunities, stands as a statistical measure of performance in a Six Sigma project. It precisely quantifies the number of defects in a process per one million opportunities for error. Establishing this metric enables assemblers and fabricators to pinpoint inefficiencies with remarkable accuracy, offering a clear path to enhance quality and impress clients. By adopting DPMO standards, craftsmanship elevates, and the likelihood of customer dissatisfaction markedly decreases.
Definition and Relevance
DPMO signifies a crucial performance indicator within the Six Sigma methodology, zeroing in on defect frequency. It represents the standard measure for evaluating the quality of a process.
In the realm of Six Sigma, DPMO offers a quantifiable target for improvement. It sets a high benchmark for perfection, often aiming for fewer than 3.4 defects per million opportunities.
Given its rigorous standards, Six Sigma's DPMO necessitates meticulous error analysis. Each defect becomes an opportunity for rectification, ensuring a reduction in waste and heightened process optimization.
Adoption of the DPMO metric is central to achieving operational excellence. It transforms abstract quality concepts into actionable data, becoming a beacon for continuous improvement.
Understanding DPMO is fundamental for assemblers and fabricators seeking an edge in today's competitive market. Mastery over this metric can translate into unparalleled product quality and customer satisfaction.
Calculation Mechanics
To comprehend DPMO calculations, one must distinguish defects from defective units. A singular unit may harbor multiple defects, skewing the accuracy of simplistic defect metrics.
The DPMO formula rigorously estimates defects per opportunity. Precision here is paramount for reliable results reflecting true process quality.
Firstly, total defects within a sample must be tallied. This involves scrutinizing each unit (potentially containing multiple discrepancies) to catalogue every individual shortcoming.
In parallel, calculate the number of inspection opportunities per unit. This varies across products, influenced by complexity and predefined quality criteria.
Next, multiply the number of units inspected by the number of opportunities per unit. This result conveys the total number of opportunities for defects to transpire within the sample.
Finally, divide the total defects by total opportunities and multiply by one million. The quotient articulates the DPMO rate, benchmarking the defects' prevalence within the process.
Comparing DPMO to Other Metrics
DPMO offers a nuanced view of quality distinct from other common metrics.
- First Pass Yield (FPY): Measures the percentage of units that pass the first inspection without rework.
- Overall Equipment Effectiveness (OEE): Captures the percentage of manufacturing time that is truly productive.
- Process Capability Index (Cpk): Evaluates how well a process meets specification limits.
- Total Quality Management (TQM): An overarching philosophy advocating for continuous improvement in all aspects of a business.
It facilitates a granular examination of process efficiency and defect occurence.
Understanding DPMO in the context of these metrics provides a comprehensive quality landscape.
Achieving Six Sigma DPMO Targets
Six Sigma DPMO represents an apex of quality, with 3.4 defects per million opportunities as the gold standard. Achieving this level of near-perfection requires unwavering dedication, sophisticated analysis, and a cultural commitment to quality excellence.
In pursuit of Six Sigma DPMO, organizations must meticulously employ tools such as Failure Mode and Effects Analysis (FMEA), Statistical Process Control (SPC), and Control Charts. These instrumentalities are pivotal in identifying areas of improvement, monitoring process stability, and maintaining operational rigor to mitigate defects and optimize performance.
The journey toward “Six Sigma” and “Zero Defects” are not mere slogans but mandates that necessitate transformative strategies. Only through continuous improvement, prevention-focused methodologies, and an empowered workforce can this echelon of quality be actualized.
Understanding Sigma Levels
Sigma levels represent the ability of a process to produce defect-free outputs. To quantify the performance, we refer to standard deviations, a statistical measure indicating the spread or dispersion within a set of data. As sigma levels increase, the defect rate decreases, which denotes a higher quality process.
Each sigma level corresponds to a specific number of defects per million opportunities (DPMO). An increase in the sigma level means fewer defects and closer adherence to customer specifications.
Central to Six Sigma methodology, sigma levels provide a metric for comparing different processes or entities. They serve as benchmarks for quality and are often a litmus test for process improvement. Attaining higher sigma levels indicates a more capable and controlled process mitigating variations which may lead to defects.
The quest for higher sigma levels requires empirical analysis and a strategic approach to process improvement. Organizations aim to progress from lower to higher sigma levels as a route to reduced variability and enhanced customer satisfaction. It is an evolutionary process, where continuous refinement and incremental gains aggregate into significant enhancements in quality and efficiency.
Tools for DPMO Improvement
The DMAIC (Define, Measure, Analyze, Improve, Control) framework guides process improvement initiatives. As a rigorous data-driven methodology, it requires evidence-based approaches to drive down DPMO.
Fundamental to Six Sigma is a suite of statistical and quality management tools called the "Seven Basic Quality Tools." Ranging from Cause-and-Effect Diagrams to Control Charts, these instruments facilitate insight into process performance, identifying the root causes of defects, and developing methods for improvement. Proficiency in applying these tools ensures a structured and effective reduction in defects, subsequently lowering DPMO metrics.
Pareto Charts and Process Mapping stand as additional tools pivotal to DPMO improvement. These visual tools enable the identification of the most significant opportunities for enhancement, charting a course towards a more refined process with fewer defects and higher quality.
Moreover, Advanced Statistical Software applications are essential for analyzing complex data sets. Such technology allows teams to extrapolate meaningful patterns, simulate process changes, and predict outcomes. Investing in these software tools accelerates the journey toward Six Sigma excellence, reducing DPMO by providing insights that are not readily apparent through manual analysis. Ongoing training in their use is vital to maximize their potential to uncover ways to innovate and elevate product quality.
Case Studies of Successful Implementations
The integration of Six Sigma methodologies has poignant results, reshaping entire industries.
- General Electric: Capitalized on Six Sigma, reporting a savings of over $2 billion.
- Motorola: The progenitor of Six Sigma, significantly reduced production defects.
- Honeywell: Integrated Six Sigma principles, enhancing their manufacturing efficiency.
- Ford Motor Company: Applied Six Sigma tactics, culminating in profound annual savings.
- Toyota: Implemented Six Sigma and Lean principles, leading to exceptional quality and efficiency.
In sectors ranging from automotive to electronics, success stories abound.
These achievements highlight Six Sigma's transformative potential when meticulously executed.
Six Sigma Certification Insights
Assembling and fabricating professionals seeking to enhance their proficiency in quality management may consider Six Sigma certification as a pivotal step in their career development. Certification often entails a rigorous curriculum, with varying levels of expertise recognized by designations such as Yellow Belt, Green Belt, Black Belt, and Master Black Belt. By attaining certification, individuals not only validate their competencies in identifying and eliminating defects but also demonstrate a commitment to continuous improvement—a quality highly revered in manufacturing arenas. This mastery of Six Sigma methodologies can be a distinctive advantage in a competitive marketplace, signaling to customers a dedication to operational excellence and superior quality control.
Overview of Six Sigma Belts
Six Sigma Belts categorize levels of expertise within the methodology's framework, akin to the ranking system in martial arts. Each belt signifies a deepening mastery of Six Sigma principles, tools, and processes, culminating in a hierarchical structure of qualifications that convey proficiency and leadership in quality management.
Yellow Belts provide foundational knowledge, serving as a stepping stone within the Six Sigma certification journey. They understand basic practices and support larger project teams.
Green Belts exhibit a more advanced grasp, typically leading smaller projects or playing supportive roles in larger initiatives. They analyze and solve quality problems, employing statistical analysis tools.
Black Belts possess a comprehensive understanding of Six Sigma, spearheading complex projects and coaching Green and Yellow Belts. Their expertise includes strong problem-solving skills and the ability to lead cross-functional teams.
Master Black Belts represent the pinnacle of Six Sigma proficiency. They serve as mentors to Black Belts and drive strategic initiatives, often shaping the direction of Six Sigma deployment within an organization.
Ultimately, the Six Sigma Belt system delineates an individual's capability to contribute to process improvement initiatives. Ascending the belt hierarchy signifies growing leadership responsibilities and the ability to impart Six Sigma methodologies throughout various levels of an enterprise.
Steps to Six Sigma Certification
To begin your Six Sigma journey, identify which belt level aligns with your current skills and career goals. Entry-level practitioners often start with a White or Yellow Belt.
Select a reputable Six Sigma certification body or training program that suits your chosen level. Accreditation matters, so be diligent in your selection.
It is imperative to invest time in mastering Six Sigma methodologies, statistical tools, and project management principles pertinent to your belt level. This should be complemented by practical experience with quality-improvement projects.
Successfully passing the certification exam is not the endpoint; it's a launchpad. Continuing education and direct application of Six Sigma principles in your work will sustain your proficiency. Over time, you can progress to higher belts, which necessitate acquiring an advanced mastery of Six Sigma practices and demonstrating leadership in complex projects.
Preparing for Six Sigma Exams
When planning your study strategy, consider the belt level's body of knowledge, as concepts, tools, and problem-solving methods vary greatly between belts, reflecting a progressively sophisticated understanding of Six Sigma principles.
Establish a regular, focused study schedule to internalize the complex statistical methodologies central to the Six Sigma approach.
Treat practice exams as essential tools, leveraging them to gauge your comprehension of the Six Sigma framework and to sharpen your test-taking strategies.
Continuous immersion in Six Sigma material is critical - engage with textbooks, case studies, online modules, and Six Sigma practitioners to deepen your understanding of the methodology.
Combine theoretical study with practical application, aligning your hands-on project work with the specific knowledge areas of the exam, thus ensuring you're not only adept at the concepts but at their practical implementation as well.
Ultimately, to excel on the Six Sigma exams, unwavering dedication is key. Proper preparation bridges the gap between academic understanding and the strategic acumen necessary for real-world problem solving.
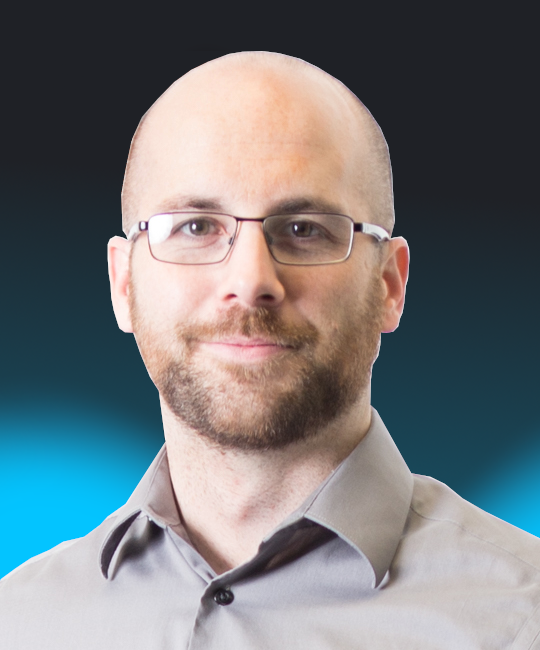
Ben Marsh
I've spent my career in Manufacturing, and can't stop trying to make things more efficient. At home, I am a master Lego builder with my son.