In a world where everyone wants more for less, the burden often falls on Manufacturers to prioritize new ideas to lead to greater cost saving opportunities.
Lean Manufacturing Principles
Lean manufacturing methods focus on efficiency, both in terms of processes and employee productivity and should be a core value in all organizations. Lean implementation stimulates the perfect balance between minimal waste and maximum output, leading to a drastic cut in operational costs and rapid ROIs.
Lean manufacturing methods provide a tangible competitive edge, optimizing operations for minimal waste, increased output, and superior product quality, thus enhancing customer satisfaction and retention.
In today's technologically advanced factories, lean manufacturing is revolutionizing operations. By encouraging continuous improvement and valorizing employee feedback, it enhances the production process, enabling assemblers and fabricators to impress customers with high-quality products and swift delivery times.
Implementing Just-In-Time (JIT) Inventory
Don't let potential cost savings slip through your fingers. Embrace Just-In-Time (JIT) inventory—a cost-effective technique revolutionizing assembly lines and proving instrumental to thwart threats of overproduction. Let's review its benefits.
- Substantial savings: Minimize overhead costs by ordering only what's necessary, and when it's needed.
- Increased efficiency: JIT systems streamline production by eliminating unnecessary inventory proliferation.
- Improved cash flow: By avoiding stockpiling, funds can be successfully funneled into other business growth areas.
- Enhanced supplier relationships: Regular, smaller orders pave way for maintaining consistent supplier interactions.
- Reduced waste: With JIT, you order inventory right when required, reducing chances of spoilage or outdated stock.
- Risk mitigation: Overproduction risks are rendered irrelevant because production happens based on real-time demand.
Reducing Waste with Six Sigma Methodology
In the drive to reduce waste and enhance profitability, Six Sigma methodology has outlined a systematic, data-driven approach that allows assemblers and fabricators to reach a new level of precision, consistency, and quality.
- Identifying and eliminating process variations with Six Sigma's DMAIC (Define, Measure, Analyze, Improve, Control) model
- Adopting quality management tools such as Pareto charts, fishbone diagrams, and process maps
- Creating a culture of continuous improvement, fostering employee engagement
- Minimizing material usage and scraps by optimizing processes
- Leveraging data analysis for predictive maintenance, avoiding breakdowns and delays
Streamlining Production Processes with Value Stream Mapping
Value Stream Mapping is a highly recommended method for uncovering inefficiencies in your production line, providing a clear road map for achieving greater efficiency. This pivotal tool will help fine-tune fabrication efforts while illuminating the areas where your assembly lines can be improved.
- Identifying issues in real-time: Value Stream Mapping helps audit problems in your manufacturing process as they occur, allowing you to take immediate actions.
- Minimizing waste: This method exposes redundancy and waste in your assembly line, enabling you to make necessary adjustments.
- Enhancing productivity: It provides an opportunity to optimize work processes and eliminate activities that do not add value.
- Promoting continuous improvement: This tool encourages a culture of routine upgrades, helping your assembly line stay on the cutting edge of efficiency.
Digital Automation
In the past, automation in manufacturing was primarily focused on the use of physical equipment to streamline processes. However, with the advancements in technology, there are now multiple new opportunities to automate various aspects of manufacturing beyond just the physical realm.
One such area is data collection and analysis. By implementing digital software systems, you can automate the collection of data from different stages of the production process. This not only saves time but also ensures accuracy and consistency in data collection. Additionally, these systems can provide real-time analytics and insights, allowing you to make data-driven decisions and identify areas for improvement.
Another aspect that can be automated is the tracking of quality records. Instead of relying on manual record-keeping, digital software systems can automate the recording and tracking of quality data. This not only reduces the chances of errors but also provides a centralized and easily accessible repository for quality records. This automation can help streamline quality control processes and ensure compliance with industry standards.
Furthermore, automation can also help reduce or even eliminate the need for paper-based documentation. By digitizing processes and implementing electronic documentation systems, you can significantly reduce paper usage, storage costs, and the risk of document loss or damage. This not only contributes to cost savings but also aligns with sustainability initiatives.
Implementing Automated Quality Control Systems
High quality no longer needs a high labor cost to accomplish, by embedding Quality Control systems directly into digital work instructions. These systems allow you to dynamically adjust quality checkpoints to appear more or less frequent due to the specific problem - instead of relying on factory-wide generic guidelines.
By enabling real-time fault detection, you will experience a reduction of rework and instead increase your throughput rates. Eliminating manual errors, your production pace will accelerate and simultaneously ensure consistent product quality.
These systems offer assemblers a paradigm shift from traditional time-consuming quality checks to real-time precision. The resulting savings in manpower and resources are significant, making it an investment worth considering for modern manufacturers.
Energy Efficiency Strategies
Elevating energy efficiency distinguishes itself as a pivotal component for generating manufacturing savings. Incorporating efficient practices caters to both sustainability criteria and improved financial outcomes.
Seizing the potential of energy efficiency enables drastic cost reductions in the manufacturing industry. The conscious reconfiguration of processes towards energy optimization epitomizes a strategic approach for manufacturers.
Optimizing Equipment and Machine Settings for Energy Savings
Unlocking potential savings starts with machine optimization, focusing primarily on energy efficiency. Conscious calibration and setting adjustments on equipment can vastly decrease energy consumption, thereby reducing energy costs significantly.
Optimal equipment settings play a driving force, leading to major energy savings. These settings allow machinery to operate at peak efficiency, translating into decreased power usage. Ultimately, enterprises experience significant cost savings in the long term.
Investing in Energy-Efficient Machinery
The transformation to energy-efficient machines in manufacturing is financially viable. Initial expenses are offset by significant savings in energy consumption and maintenance costs in the long run.
A shift to energy-efficient machinery marks a pivotal moment in manufacturing. These systems not only reduce energy use but also improve productivity with less downtime.
This revolution has positioned manufacturers ahead of the curve. They're delivering better work while maintaining environmental integrity, giving them a competitive edge in today's eco-conscious business landscape.
Implementing LED Lighting Systems
Incorporating LED lighting systems can illuminate more than just your manufacturing spaces—it can brighten your profit margins. These systems, known for their energy efficiency, can significantly reduce your energy consumption and operational costs.
Switching to LED lighting is not just an ecological decision, it's financially smart. The long-term cost reduction associated with these systems greatly outweighs the upfront expenses, making it an ideal choice for cost-conscious assemblers and fabricators.
Supply Chain Optimization
Leveraging an intelligent supply chain doesn't only streamline the operations but also anchors cost reduction. Implementing smart supply chain practices like using predictive analytics, AI, and IoT can help manufacturers better predict demand, optimize inventory management, thereby reducing carrying costs.
Addressing potential gaps in supply chains can result in considerable savings. Implementing strategies such as vendor-managed inventory, advanced planning, and scheduling systems, companies can minimize delays, better manage their production schedules, and ultimately cut costs. Efficient supply chain operations are key in realizing cost reductions while maintaining high levels of product quality and customer satisfaction.
Establishing Strong Supplier Relationships
Strategic alignment with your suppliers elevates beyond mere transactional exchanges, enabling mutual value creation. Deepening these partnerships encourages joint problem-solving, innovation, and shared success, transforming your supply chain into a competitive advantage.
Investing in supplier relationships can result in significant cost savings. The mutual trust built through these bonds may speed up response times, reduce downtime, and ensure timely deliveries, easing fiscal tension.
Furthermore, a strong supplier bond not only ensures supply continuity but can also open doors for negotiation, offering favorable prices or payment terms. An excellent supplier relationship fosters financial resilience, operational efficiency, and strategic growth.
Implementing Vendor-Managed Inventory (VMI)
Have you explored Vendor-Managed Inventory (VMI)? VMI liberates manufacturers from inventory management, enabling seamless production and revenue maximization.
Recognize VMI as the unseen cost-saving hero in manufacturing. It significantly reduces procurement related costs, directly influencing your bottom line.
VMI offers a fresh perspective, shifting inventory management to suppliers. This approach curbs unexpected stockouts and enhances customer satisfaction.
Utilizing Advanced Planning and Scheduling (APS) Systems
Advanced Planning and Scheduling (APS) systems, when properly implemented, act as a smart strategy for manufacturing, offering substantial cost savings. Such systems streamline operations, minimizing downtime and wasteful procedures.
APS systems are precision tools that drive down manufacturing costs by deftly coordinating production activities. They allow for seamless scheduling, ensuring operations keep pace with demand and resources are optimally utilized.
In addition, APS systems provide real-time visibility into the manufacturing process. This ability to monitor activity enables quick adjustments, sidestepping potential bottlenecks and reducing costs associated with idle machinery or inventory.
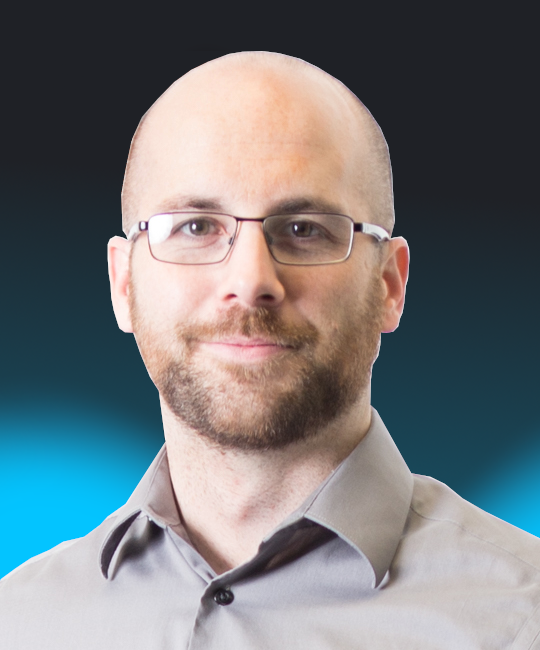
Ben Marsh
I've spent my career in Manufacturing, and can't stop trying to make things more efficient. At home, I am a master Lego builder with my son.