Intelligent Work Instructions represent a significant leap forward in the evolution of Standard Operating Procedures. The advancements in this field are truly remarkable. Gone are the days of Engineering Prints and paper-based instructions in binders, or even PDF versions displayed on digital screens. These traditional methods lack intelligence, often rely on the expertise of individual operators, are prone to human error, and fail to capture valuable production data.
The adoption of Intelligent Work Instructions brings about transformative benefits, including:
- Reduced Training Time
With intelligent instructions, the learning curve is greatly shortened. Operators can quickly grasp complex processes and procedures, leading to faster onboarding and increased productivity. - Lower Cost of Quality
By providing precise and error-proof instructions, intelligent work instructions minimize costly errors and rework. This translates to significant savings in terms of time, resources, and overall quality control. - Increased Production Capacity
Intelligent work instructions optimize workflow and eliminate bottlenecks. By streamlining operations and ensuring consistent execution, production capacity can be enhanced, leading to higher output and improved efficiency.
Embracing Intelligent Work Instructions unlocks a world of possibilities for manufacturers, empowering them to achieve operational excellence, enhance training processes, and drive overall productivity.
Reducing Training Time
Clear instructions play a crucial role in accelerating operator training. At Scout Systems, our customers consistently experience a remarkable reduction of nearly two-thirds in the time it takes for new operators to reach the productivity level of seasoned veterans. Let's take a closer look at an example that illustrates this progress:
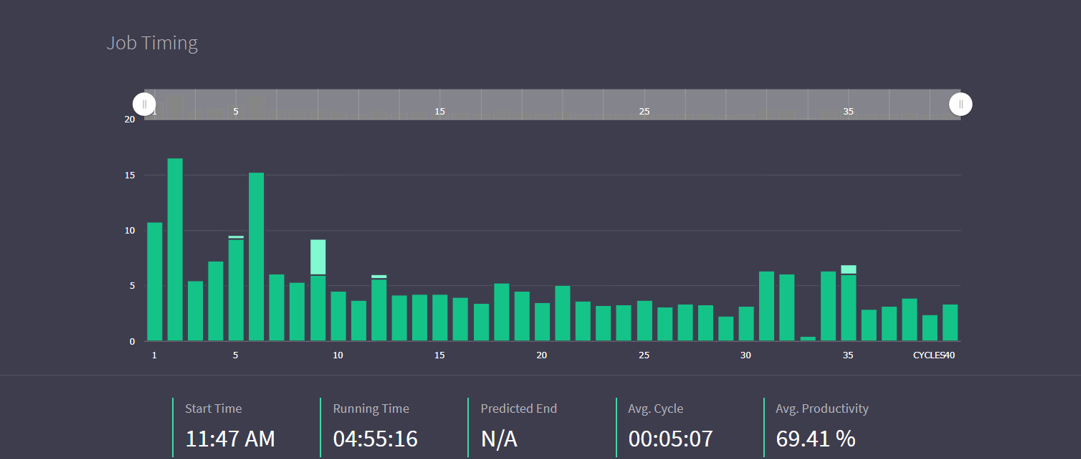
In the case above, the operator was able to achieve the pace of a veteran and maintain it by the 9th unit built. This remarkable progress demonstrates the effectiveness of our clear and comprehensive instructions in expediting the learning process.
What leads to this Rapid Training?
Accelerating training is essential for boosting productivity and efficiency in your operations. Let's dive right in and explore the key benefits of our training offerings:
-
Better Organization: Our platform provides a centralized location for all production information, making it quick and easy to access and understand what work needs to be done. No more searching through multiple sources or documents.
-
Clear Setup Instructions: Operators can instantly view the tools, materials, and setup requirements for each work order, ensuring a smooth and efficient preparation process. Our instructions leave no room for confusion.
-
Step-by-Step Work Instructions: Each task is presented in a clear and concise manner, with visual callouts and accompanying text. For more detailed guidance, we even offer the option to embed instructional videos, providing a comprehensive learning experience.
-
In-Line Quality Checks: Our platform empowers operators to perform in-line quality checks, verifying parts, validating dimensions, and capturing pictures of work in progress. This ensures that quality standards are met and maintained throughout the production process.
-
Call for Help: With just a simple button press, operators can request assistance when needed. Leads and supervisors can monitor operator activities remotely and receive real-time notifications if any delays or issues arise, enabling timely intervention and support.
Lowering the Cost of Quality
Traditional methods of improving Quality can often come with increased costs. This is because most Quality improvements include more inspections, more data collection, and more data entry. A huge benefit of Intelligent Work Instructions is that all of those methods and others can become automated.
New forms of Automation
-
Revision Control: Say goodbye to the hassle of managing and updating multiple versions of your work instructions. With our platform, every time an update is made, all versions accessible to the production floor will automatically be updated to the most recent release. No more searching for and updating outdated prints. Stay organized and ensure everyone has access to the latest instructions.
-
Test Integration: Seamlessly connect your test equipment to our platform and streamline the testing process. Operators can validate passing test results directly within Compass, eliminating the need for manual documentation or buddy checks. Our system ensures that operators cannot proceed unless they receive a passing signal, enhancing efficiency and accuracy.
-
Data Integration: Harness the power of your production data with our seamless data integration capabilities. All production data is collected and processed, providing valuable insights for analysis and decision-making. Utilize our APIs to effortlessly send data to third-party platforms, eliminating the need for manual review of data tables and tedious result updates. Unlock the potential of your data and leverage it to drive improvements and optimize your operations.
Increasing your Production Capacity
There are multiple strategies you can employ to increase your production capacity, tailored to the specific nature of your factory operations. These strategies can be broadly categorized into two approaches: reducing waste and improving efficiency.
Reducing Waste
A common method of reducing waste is to measure production stops so that changes can be deployed to reduce.
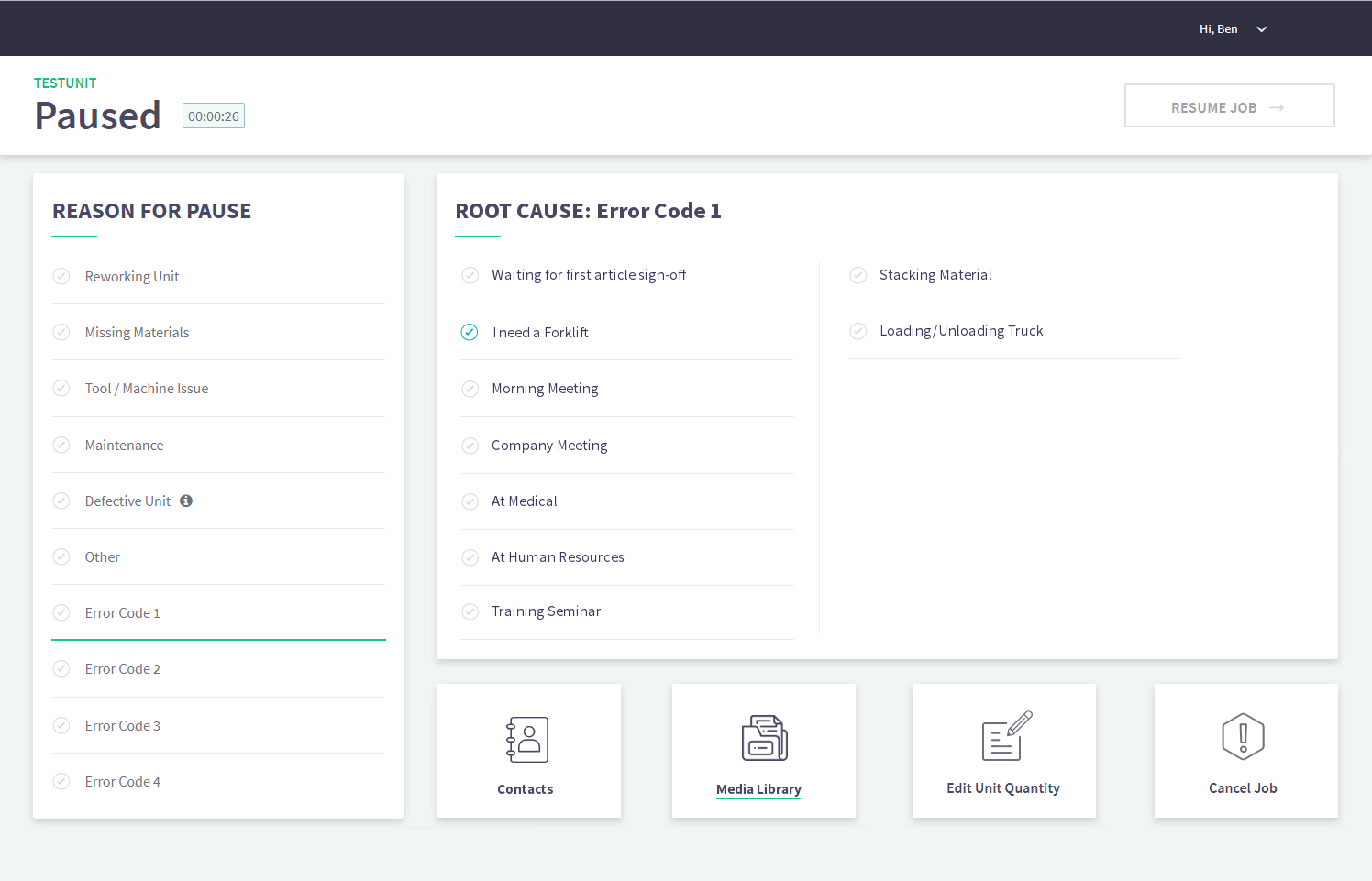
When production stops occur, your operators can easily record the downtime by pressing the 'PAUSE' button within Compass. The system will promptly begin to track and record the precise time lost during the stoppage.
To delve deeper into the root issues behind production stops, you have the option to create Root Cause problems. These problems can be associated with specific production stoppages and help identify the underlying reasons for the interruptions. By pinpointing the root causes, you can implement targeted solutions to minimize or eliminate similar issues in the future.
Discovering Hidden Waste
Waste can take various forms and may not always be apparent with traditional tracking systems. With Scout Systems, you gain a remarkable advantage as every action is meticulously recorded and analyzed throughout each production order.
This level of detailed tracking allows you to zoom into your cycle times, providing valuable insights into your production process. By examining the data, you can pinpoint specific steps that may be causing delays or inefficiencies, helping you identify opportunities for improvement.
In the example above, we are analyzing the individual step times required to build a product. The blue bars represent the Average Time taken for each step, providing a clear understanding of the typical duration for each task. Alongside the blue bars, gray lines overlay to illustrate the Standard Deviation.
The Standard Deviation is a crucial metric that reveals the variability or spread of data around the average. In this context, it indicates how much your operators deviate from the average time taken for each step. A larger Standard Deviation suggests that your operators struggle to maintain a consistent pace, leading to more significant variations in their performance.
Identifying steps with larger Standard Deviations can be instrumental in pinpointing areas where operators may encounter challenges or inefficiencies. By focusing on these steps, you can provide targeted support, training, or process improvements to help your operators achieve a more consistent and efficient workflow.
Improving Efficiency
Though reducing Waste often leads to improved efficiencies, utilizing Intelligent Work Instructions can provide even more opportunities to benefit from.
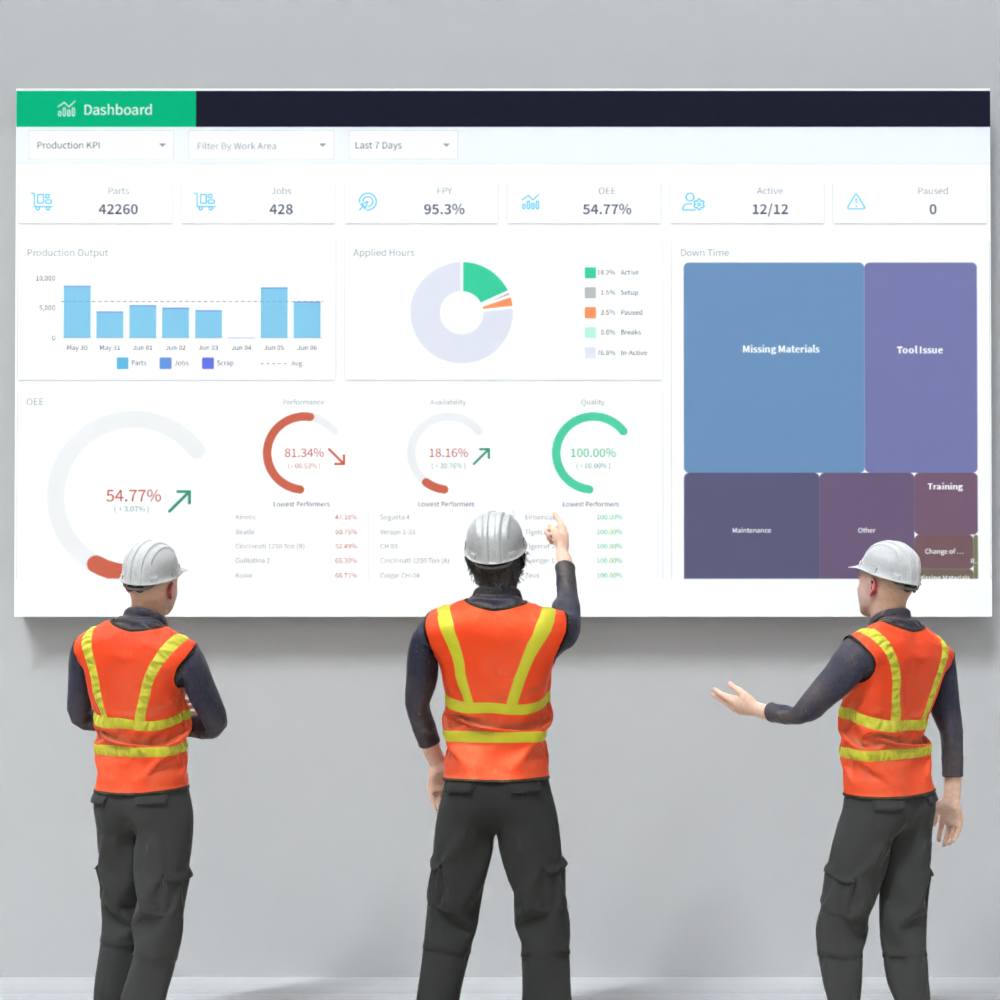
Enabling your Production Supervisors with access to real-time Production Key Performance Indicators (KPIs) is a game-changer in making informed decisions to enhance production flow. Among the most critical metrics is Overall Equipment Effectiveness (OEE), which provides a comprehensive assessment of equipment performance and utilization.
What sets Scout Systems apart from other SaaS offerings is our unique implementation of OEE even in non-equipment cells. In our Reports, we refer to it as Overall Station Effectiveness (OSE), reflecting its applicability and value across various production areas beyond traditional equipment-centric metrics.
Overall Station Effectiveness (OSE) is a powerful metric calculated by considering three key factors: Performance (speed of production), Availability (time working compared to total time), and Quality (ratio of good parts to total parts). By multiplying these three factors, Scout Systems generates the OSE value, providing a comprehensive and accurate assessment of the station's efficiency and effectiveness.
The continuous data collection and analysis in Scout Systems ensure that OSE is dynamically adjusted to reflect real-time efforts. This means that any changes or adjustments made in the production process are immediately reflected in the OSE metric. Your Production Supervisors can instantly see the positive or negative impacts of production adjustments, empowering them to make informed decisions and respond quickly to optimize productivity.
Get Caught up in only 90 Days
The benefits of adopting Intelligent Work Instructions are indeed significant, but we understand that implementing such a transformative change can feel overwhelming. That's where our Accelerator Program comes in – it's a personalized program designed to work closely with your staff to ensure a smooth and efficient implementation of this evolution.
With the Accelerator Program, Scout Systems' experts will be by your side every step of the way. We will collaborate closely with your team, providing hands-on support to guide you through the entire process. Our focus will be on delivering the specific outcomes you've set for your organization, tailoring the implementation to meet your unique needs and goals.
By partnering with Scout Systems in the Accelerator Program, you gain access to our wealth of experience and expertise in the field. We understand the challenges and opportunities associated with adopting Intelligent Work Instructions, and we are dedicated to making the transition as seamless as possible.
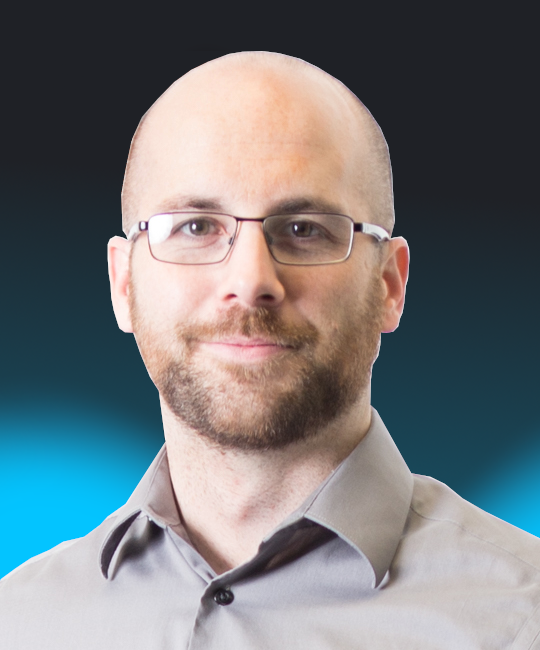
Ben Marsh
I've spent my career in Manufacturing, and can't stop trying to make things more efficient. At home, I am a master Lego builder with my son.