Feeling overwhelmed by the complexity of control systems in your manufacturing setups? In an era defined by advancements in automation, understanding and leveraging complex systems such as Advanced Process Control (APC) systems has become a non-negotiable necessity for any manufacturing operation, regardless of the industry.
APC, in a nutshell: Advanced Process Control encompasses a range of model-based software technologies, including Multivariable Predictive Control (MPC) or model predictive control, primarily aimed at directing and enhancing the efficiency of process operations. The key is in the precise representation of process dynamics through the models created.
The importance of APC systems in the manufacturing industry cannot be overstated. They are the backbone that provides supervisory control, bridging the gap between basic controls and overall process enhancement. They are the game-changers that aid in realizing sustainable profitability, quality, and operational safety, especially in a progressively Industry 4.0-aligned landscape.
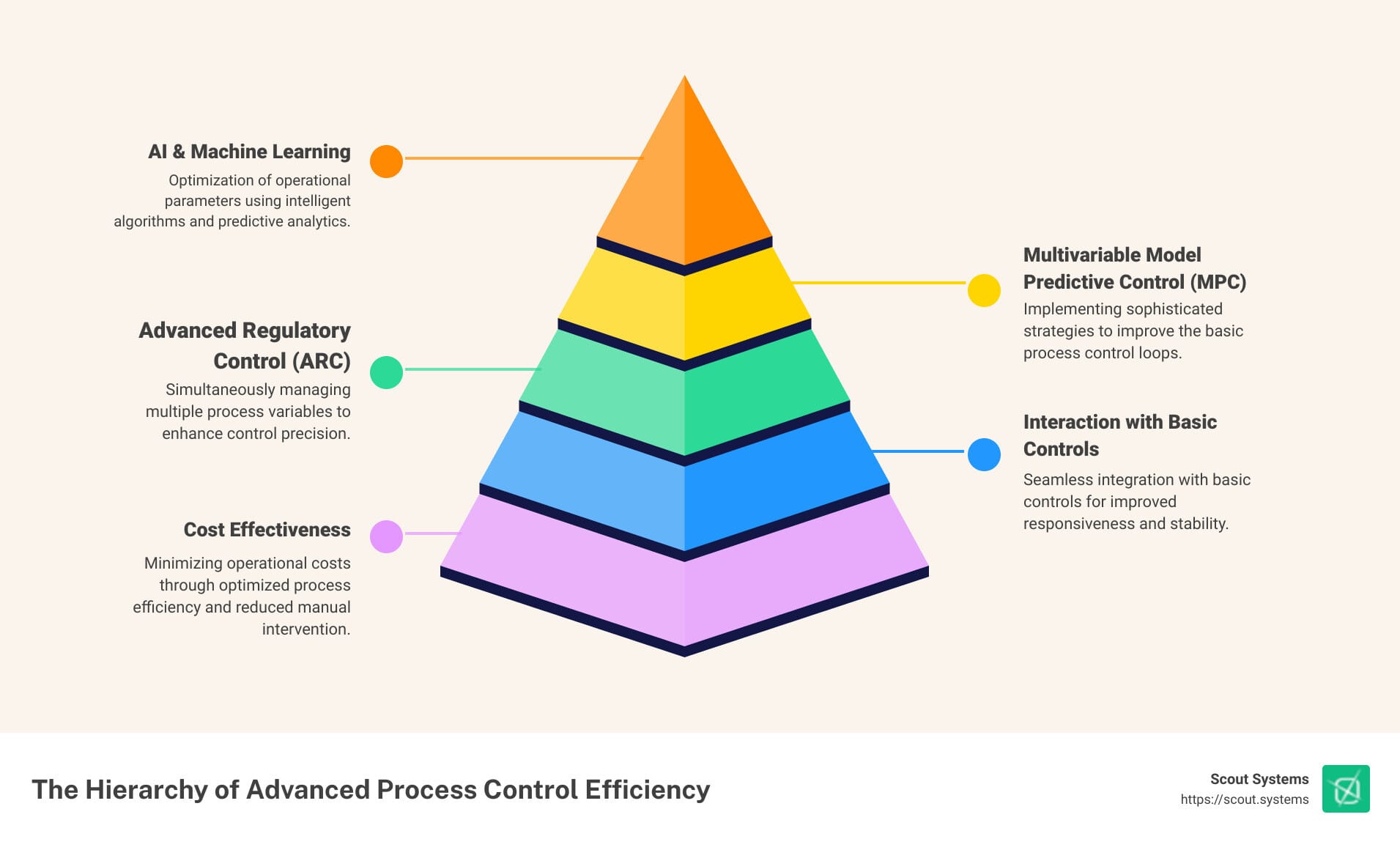
Venturing ahead, this comprehensive guide will shed light on the basics, types, and the undeniably vital role of Artificial Intelligence and Machine Learning in APC systems. You will also learn about cost-effectiveness, optimization techniques, and the promising future of APC systems, all helping you steer through 'Smart Manufacturing', gaining the Smart Factory advantage.
As experts in the field, with trackable success in Industries 4.0 adaptation, we at Scout Systems are committed to assisting you through this transformative journey to reshape your processes and translate these high-tech concepts into beneficial realities.
Understanding the Basics of Advanced Process Control Systems
In the realm of industrial operations, Advanced Process Control (APC) systems are indispensable tools that augment basic process controls, optimizing performance, and operational efficiency.
The Role of Advanced Process Control Systems in Industrial Processes
APC systems are implemented in industries that involve continuous processes, such as chemical, petrochemical, oil and mineral refining, food processing, pharmaceuticals, and power generation. These systems help manage complex industrial processes by monitoring and adjusting numerous variables to improve the overall process performance.
Unlike basic process controls that manage simple operations, APC systems provide a higher level of computational capability. They use sophisticated algorithms to predict future process behaviors and make necessary adjustments for optimal performance. This predictive capability can result in significant improvements in process efficiency, product quality, and economic performance.
The Interaction of Advanced Process Control Systems with Basic Process Controls
Advanced process control systems are not standalone entities but work in conjunction with basic process controls. The basic controls are designed with the process and facilitate basic operation, control, and automation requirements. APCs are added subsequently, often over the course of many years, to address particular performance or economic improvement opportunities in the process.
The integration of APCs with basic controls resides within the process control system, which may include a distributed control system (DCS), programmable logic controller (PLC), and/or a supervisory control computer. Basic controls reside in the DCS and its subsystems, including PLCs, while advanced controls may reside in either the DCS or the supervisory computer, depending on the application.
The Cost-Effectiveness of Advanced Process Control Systems
While the implementation of an advanced process control system might initially seem like a significant investment, it can prove to be highly cost-effective in the long run. APCs can reduce waste and increase capacity by automating high labor tasks and identifying cost-saving opportunities. As seen with our clients at Scout Systems, a well-functioning APC can result in a 5-15% increase in capacity, bringing significant operational cost reductions and boosting overall profitability.
Types of Advanced Process Control Systems
Advanced Process Control Systems come in various forms, each designed to address specific challenges in industrial processes. Let's explore five main types that are commonly used in industries today.
Advanced Regulatory Control (ARC)
Advanced Regulatory Control (ARC) refers to a set of sophisticated control strategies such as override or adaptive gain. These strategies go beyond the basic functions of a process control system, offering more complex solutions to process control challenges. ARC is often implemented using function blocks or custom programming capabilities at the DCS level. These advanced control techniques can also operate at the supervisory control computer level, depending on the application requirements.
Multivariable Model Predictive Control (MPC)
Multivariable Model Predictive Control (MPC) uses a model of the process to predict future outcomes and adjust control variables accordingly. This technology, often deployed on a supervisory control computer, identifies significant independent and dependent process variables and the dynamic relationships between them. It then uses matrix-math based control and optimization algorithms to control multiple variables simultaneously. The key requirement of MPC is that the models must be linear across the operating range of the controller.
Nonlinear MPC
Nonlinear MPC is similar to Multivariable MPC, utilizing dynamic models and matrix-math based control. However, it does not require model linearity. This allows Nonlinear MPC to accommodate processes with models that have varying process gains and dynamics, such as dead-times and lag times, offering more flexibility in handling complex process dynamics.
Inferential Measurements
Inferential Measurements, also known as soft sensors, are another type of advanced process control. These systems use mathematical models to estimate difficult-to-measure process variables based on easier-to-measure variables. This approach can significantly improve process efficiency and product quality.
Sequential Control
Sequential Control refers to the process of executing a series of operations in a specific order. This type of control is common in batch processes, where operations need to be carried out step-by-step in a predetermined sequence.
The type of Advanced Process Control system you choose for your manufacturing process will largely depend on the specific challenges you're facing. At Scout Systems, we understand the intricacies of these different systems and can help you if our solution is right for your needs, ensuring a seamless transition to Industry 4.0 and significantly reducing operational costs.
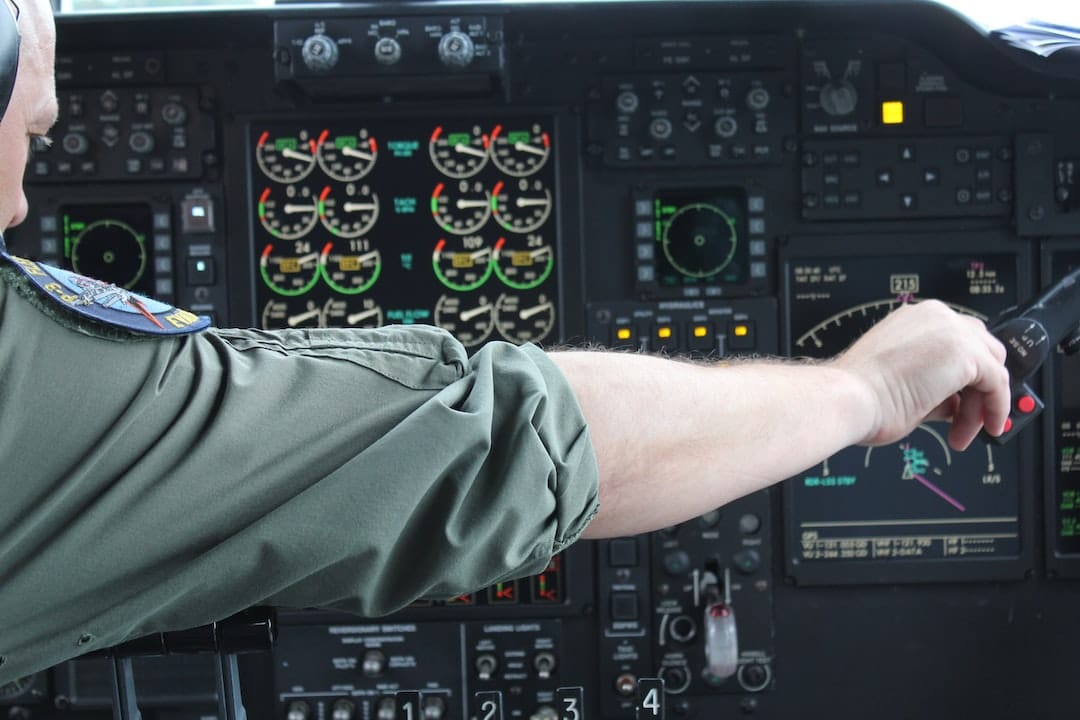
The Role of Artificial Intelligence and Machine Learning in Advanced Process Control Systems
The dawn of Artificial Intelligence (AI) and Machine Learning (ML) has ushered in a new era for advanced process control systems. They have become instrumental in optimizing operational parameters and tuning the overall system for maximum efficiency.
How AI and ML Optimize Operational Parameters in Process Control
Traditionally, the operations and logic of process control systems, particularly in oil and gas industries, were governed by physics equations and operator experience. However, this approach has its limitations. AI and ML bring a dynamic perspective to this process, analyzing operational conditions and suggesting optimized parameters.
AI and ML algorithms have the ability to learn from historical data, identify patterns, and predict future outcomes. This allows them to provide suggestions for logic parameters or give tips to operators. This can lead to significant improvements in cost efficiency, production volumes, and safety.
By integrating AI and ML into your process control systems, you're not just making your operations smarter; you're making them more adaptable to change and more responsive to new opportunities.
The Use of Machine-Learning Models and Advanced Analytics in Tuning APCs
Machine learning models and advanced analytics play a crucial role in tuning Advanced Process Control (APC) systems. These models can analyze vast amounts of data and make intelligent decisions to optimize the system's performance.
For instance, machine learning can be used to predict the optimal settings for a system under different operating conditions. This can help prevent system failures, reduce waste, and improve efficiency.
Advanced analytics, on the other hand, can provide valuable insights into the system's performance. By analyzing data from various sources, it can identify patterns, trends, and anomalies that might otherwise go unnoticed. This can help identify potential problems before they become serious, enabling proactive maintenance and reducing downtime.
However, the successful implementation of AI and ML in APC systems requires a comprehensive approach that addresses challenges across people, processes, and technologies. At Scout Systems, we believe in leveraging these advanced technologies to help manufacturers optimize their operations and stay ahead of the competition. We offer a cloud-based MES solution with built-in ML for real-time decision-making, ensuring a seamless transition to Industry 4.0 and maximizing operational efficiency.
In the next section, we will explore how to maximize the value of your advanced process control systems.
Maximizing the Value of Advanced Process Control Systems
Just as owning a high-performance sports car requires regular tuning and maintenance to keep it running at peak performance, so does an advanced process control system. With the right approach and attention to key indicators, you can not only maintain but maximize the value of your APCs. Here's how:
Regular Tuning and Comprehensive Approach for Efficient Operation of APCs
The first step towards maximizing the value of your APCs is to ensure regular tuning and maintenance of key components. This includes sensors, instrumentation, and underlying Basic Loop Controls (BLCs). A comprehensive approach that encompasses people, processes, and technologies is essential in this regard.
People: Engage operators and vendors in performance management. A comprehensive change management approach can help ensure APCs are utilized effectively and maintained in good health.
Processes: Implement digital work instructions with built-in quality assurance to maintain standardization that is proven to deliver on your customer's expectations.
Technologies: Review and improve APC design and logic. Use advanced analytics to identify the right objective function and input-output relationships.
As an example, a North American basic-materials company managed to increase zinc recovery by around 8% using this comprehensive approach.
Indicators for Identifying Opportunities for Optimization
Identifying opportunities for optimization is also crucial in maximizing the value of your APCs. Key performance indicators (KPIs) and dashboards can provide valuable insights into APC performance and health. For instance, high variability in process parameters, such as temperature or pressure, may indicate poor controls and present an opportunity for optimization.
Collaborating with APC Vendors and Prioritizing Optimization Initiatives
Last but not least, collaboration with APC vendors and prioritization of optimization initiatives can further enhance the value of your APCs. At Scout Systems, we do this by starting every project off with our Project Success Mode Effect and Analysis tool (PSMEA). Vendors often have deep technical knowledge and can provide valuable insights into potential improvements.
At Scout Systems, we believe in working closely with our customers to understand their unique needs and challenges. Our dedicated team collaborates with you to configure digital work instructions, quality assurance, and machine monitoring capabilities to your unique needs, ensuring a seamless Industry 4.0 adaptation.
The key to maximizing the value of your advanced process control system is not just about having the latest technology, but about effectively using and maintaining it. As the saying goes, "A well-tuned old instrument can outperform a poorly maintained new one."
The Future of Advanced Process Control Systems
As we look ahead, it's crucial to recognize the challenges and limitations of current Advanced Process Control (APC) systems, and explore proposed paradigms for more affordable and reliable solutions. In this journey, we'll also delve into the role of cloud-based Manufacturing Execution System (MES) solutions in the future of APC systems.
The Challenges and Limitations of Current APC Systems
Despite the significant benefits of APC systems, they're not without their challenges. The complexity of these systems, for instance, can make them difficult to operate and maintain. Moreover, they tend to cast a wide net, incorporating large matrices of variables and models, which can make the system cumbersome and increase maintenance needs.
The extensive use of feedforward models in traditional APC systems, though powerful in proactively rejecting disturbances, adds an additional layer of complexity and maintenance. This approach may not always be necessary or beneficial in all applications, especially given the reliability of simple feedback control.
Proposed Paradigms for More Affordable and Reliable APC Systems
To overcome these challenges, the industry is moving towards a new paradigm: smaller, more affordable, agile, and reliable APC systems. These systems use durable qualitative models, sans embedded optimizers, with more intuitive and succinct matrix designs.
This shift towards a more streamlined approach to APC systems focuses on automation, leveraging existing, proven, manual multivariable control operating practices. This approach can result in more manageable systems that are easier to implement and maintain.
The Role of Cloud-Based MES Solutions in the Future of APC Systems
As we, at Scout Systems, strive to make the transition to smarter manufacturing as seamless as possible, cloud-based MES solutions play a critical role. These solutions, like our own, offer personalized digital work instructions, quality assurance, and machine monitoring capabilities, all tailored to meet unique operational needs.
Cloud-based solutions also hold the promise of rapid deployment with strong momentum, allowing your staff to maintain focus on your factory while we guide you through the digital transition. The result is a realized opportunity for significant improvements in a short time span, with tangible data to validate your investment.
The future of APC systems will undeniably be shaped by the integration of these cloud-based MES solutions. They not only offer the benefits of advanced process control but also enhance operational visibility, reduce waste, and lower costs, thereby propelling manufacturing industries into the future of smart manufacturing.
As we look towards the future, it's clear that the evolution of advanced process control systems will continue to be instrumental in driving operational efficiency and productivity in the manufacturing industry. In this era of smart manufacturing, embracing these advancements is not just an option, but a necessity.
In the next section, we'll wrap up our comprehensive guide to advanced process control systems, reflecting on the importance of these systems in the current and future landscape of manufacturing.
Conclusion: The Importance of Advanced Process Control Systems in the Era of Smart Manufacturing
As we've explored, advanced process control (APC) systems play a pivotal role in the modern manufacturing landscape. From reducing operational costs to securing tribal knowledge, these systems provide a wealth of benefits that are essential in today's hyper-competitive manufacturing sector.
APC systems are not just tools, they're game-changers. In an era defined by advancements in big data analytics, machine learning, and artificial intelligence, APC systems are the key to unlocking a new level of efficiency and quality in manufacturing. They provide manufacturers with the ability to make informed decisions, identify non-value added time issues, and make necessary adjustments and improvements to increase production.
Our reliance on these systems is only set to increase as we move into the future. With the pace of new technology accelerating and many manufacturers yet to catch up to the Internet of Things (IoT), the need for APC systems is more pressing than ever. As Charles B. from Gunderson stated, "We now have an accurate accounting of the time it takes to manufacturer specific parts. We have identified non value added time issues and made adjustments and improvements to increase production."
But the transition to this new era of smart manufacturing need not be daunting. At Scout Systems, we are dedicated to making the digital transition easy and efficient. Our unique approach targets a return on investment while helping you navigate systematic changes. Our experts provide continuous guidance, allowing your staff to focus on your factory. And with our Accelerator Program, we make it possible to fast-track your digital transformation, securing your place at the forefront of innovation.
In less than 3 months, you can experience improvements that can be quantified; using the data to validate your investment. As one of our clients, Eli from Technical Cable Applications, noted, "Our experience with Scout Systems has been very much worthwhile. You will get a wealth of good data to make informed and intelligent decisions in whatever your process entails."
Are you ready to take the leap into smart manufacturing? Let's get started today and explore the potential of advanced process control systems together. The future is digital, and it's closer than you think.

For further reading, explore our products and learn more about our digital transition approach.
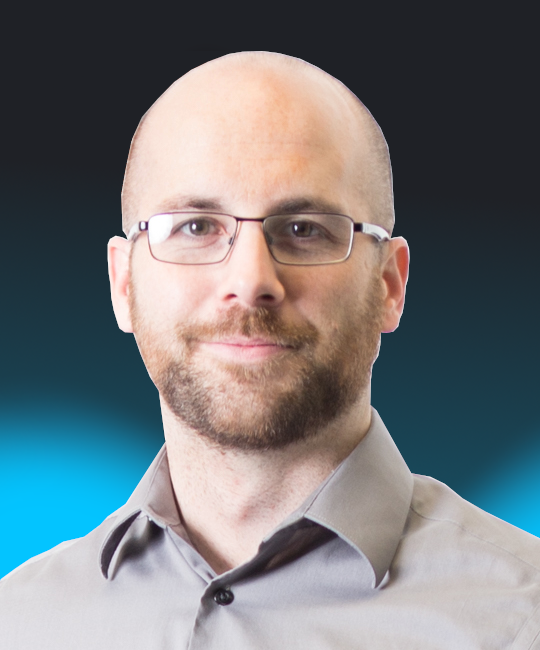
Ben Marsh
I've spent my career in Manufacturing, and can't stop trying to make things more efficient. At home, I am a master Lego builder with my son.